1950年,日本的丰田英二来到美国底特律,考察了福特公司的轿车厂。当时这个厂每个月能生产9000辆轿车,比日本丰田公司一年的产量还要多。彼时的丰田不但资金短缺,还面临着原材料供应不足的问题,与美国汽车制造业差距巨大。但是考察后,丰田英二在他的考察报告中提出“那里的生产体制还有改进的可能”。
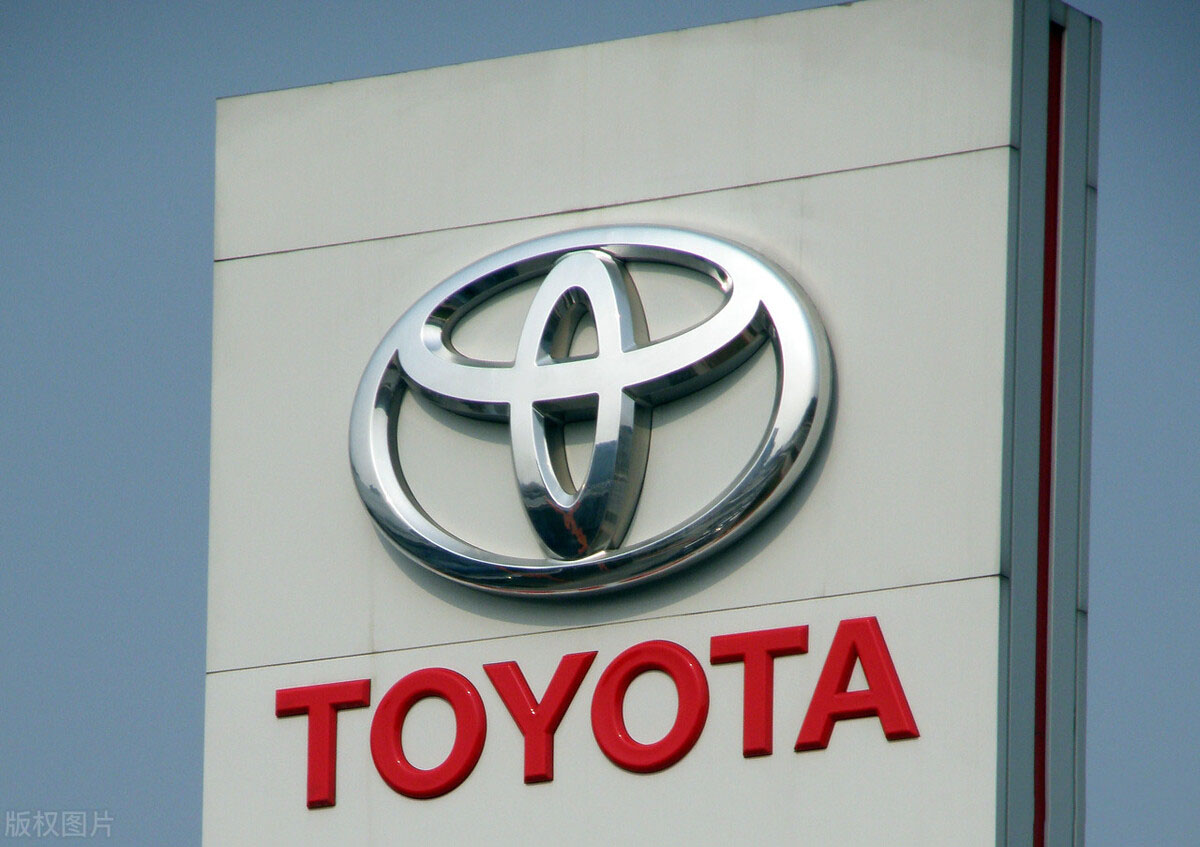
精益生产之道,到了变革的时候?
丰田公司的创始人丰田喜一郎提出:降低成本,消除不必要的浪费。他提出最好把每个必要的零部件,非常准时地集中到装配线上,工人每天只做必要的数量。大野耐一践行了这个理念,在汽车的生产组织、管理方面中逐渐形成了精益生产方式,其核心就是准时生产(准时制Just-in-Time)。
JIT管理(Just In Time),又称即时管理,零库存管理。其主要思想是“在需要的时间,使用需要的资源,生产需要的产品”。生产原料及产品实现零库存。1973年,爆发了全球石油危机,当时靠进口原材料发展经济的日本受到了严重的冲击。企业在原材料成本难以降低的情况下,只能从采购、库存、运输等方面着手,降低这些环节的费用,提高利润,JIT经由丰田公司提出,取得了不错的效果。随后,其他许多日本公司也采用这一技术,为日本经济的发展和崛起做出了重要贡献。
很多西方企业家通过研究,认为JIT技术和管理思想是日本企业的制胜法宝,通过不断学习研究,将它用于生产管理、物流管理等方面。1987年已有25%的美国企业应用JIT技术,到现在,绝大多数美国企业仍在应用JIT。
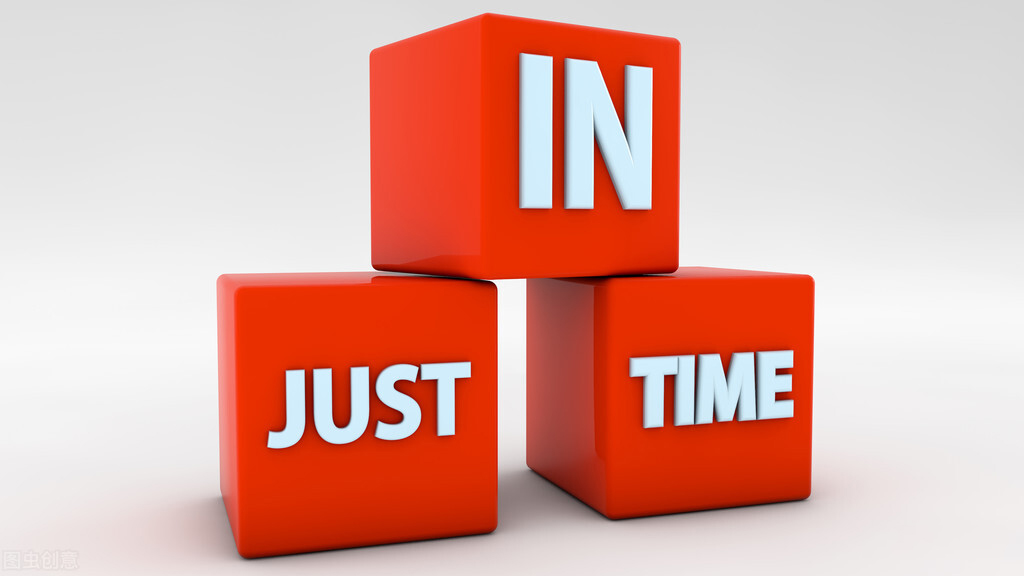
精益生产之道,到了变革的时候?
精确的库存控制、送货和生产,苛刻的质量控制体系帮助丰田把库存和成本降到了最低。2020年,丰田汽车高居《财富》全球五百强第10名,年销量超过1000万辆。
但到了2021年,形势突变。8月,丰田公司发布消息称,受疫情引发的零部件供应不足的影响,在日本本土14家工厂共计27条生产线临时停工,减产规模约36万辆。事实上,2011年福岛地震和海啸后丰田汽车就加强了半导体芯片的储备,比起其他汽车厂商,丰田受到芯片短缺的影响较小。但是,“缺芯潮”愈演愈烈,对西方企业界奉为圭臬的JIT提出了严峻的挑战,零库存显然不能应付突发状况,特别是已持续近两年的新冠疫情仍未得到有效控制下,精益生产系统显得很脆弱,没有缓冲区,不够安全和保险。
上个世纪70年代,汽车电子元件的成本占比大约为5%左右,2005年汽车电子元件的成本比例大概增长至15%左右,而2019年一辆新车的芯片成本平均为329美元。因为缺芯导致汽车业2021年营收预计将减少千亿美元。小小的芯片缺扼住了汽车制造厂商的咽喉,这个问题已经引起了人们越来越多的反思:精益生产之道在风险控制方面是比较脆弱的,或许已经到了该变革的时候了。