QCC可以让在现场各部门的管理人员相互切磋、不断上进,还有利于上下级进行沟通和相互理解,营造一个愉快的工作氛围和现场。QCC过程中,提出问题,找出缺点,然后以科学有效的方式方法去改进,为创新提供了更好的发展平台。
8D是解决不明原因质量问题的一种方法,从众多因素中找出产生质量问题的真正原因,达到改善和提升质量目的。
QCC和8D的实质是一样的,均是质量管理工作的一部分、一种工具、一种行之有效的质量改进活动。
1、QC活动的产生与发展
QC活动的产生源于1962年日本首创的QC小组,开展QC小组活动在日本作为全面质量管理的一项重要工作,对于质量管理提升产品品质起到了巨大作用。日本产品的品质在二十世纪七、八十年代获得了世界消费者的认可,“日本货”成为产品过硬品质的代名词。
于是,世界各地都相继取经开展QC活动。中国从1978年开始推行全面质量管理和开展QC小组活动至今,在各企业中,每年都会活跃多个QC小组。
QC小组是质量管理小组的简称,也称为品管圈活动QCC(Quality Control Circles),是“在生产或工作岗位上从事各种劳动的职工,围绕企业的经营战略、方针目标和现场存在的问题,以改进质量、降低消耗、提高人的素质和经济效益为目的组织起来,运用质量管理的理论和方法开展活动的小组。”
企业通过开展形式多样的QC活动,可有效解决企业发展过程中的管理和技术上的诸多难题。
2、组建QC小组并开展活动
QC小组活动是实施全面质量管理的有效手段,是全面质量管理的群众基础和活力源泉,通过QC小组的形式,把广大基层员工发动和组织起来,不断发现问题、分析问题和解决问题,在开展活动中充分发挥员工的积极性、主动性和创造性,进行自我学习,相互启发,共同研究,解决共同关心的问题,从而实现自我控制、自我提高的目标。
QC小组采取自愿结合的原则,以技术人员和操作工人相结合的3~10人组成跨部门的小组,利用工作间隙或业余时间通过组织学习、分析实践等,按照PDCA戴明螺旋上升环程序展开活动解决实际问题。
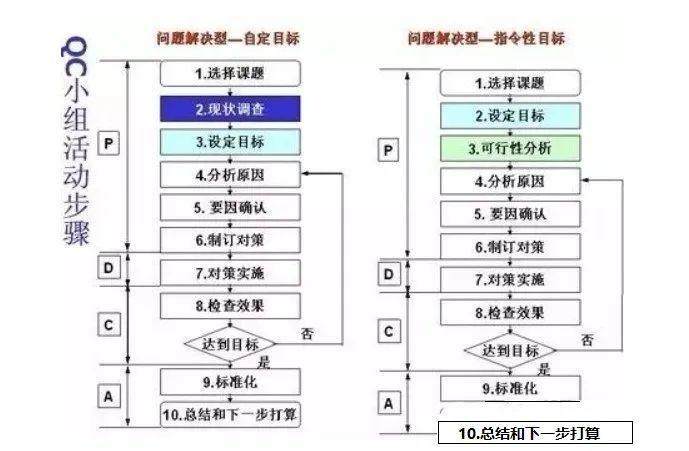
QC的整个过程、步骤
1、课题选择
一般来说,选题以企业技术、管理的薄弱点为突破口,课题宜小,从其名称应一目了然地看出是要解决什么问题,不可抽象。必须说明选题理由,直接展示和写出为什么选这个课题?为什么制定这个目标?问题的症结在哪里?
课题的名称应注意不要将对策加在课题名称里,例如“应用***设计,提高***质量”,“运用***技术,降低***消耗”。因为在活动初期选择课题期间还没有制定出对策。
2、现状调查
现状调查要以事实为依据,用数据说话。对取得的数据整理、分类,通过质量管理统计方法/工具(如调查表、简易图表、排列图、亲和图、直方图、控制图、散布图、分层法、头脑风暴法、水平对比、流程图等)的运用进行分析,以便找到问题的症结所在,从而印证课题选择的理由。
现状调查的主要目的是找出主要问题,主要问题最多不能超过两个,这是为以后的原因分析埋下伏笔。
3、设定目标
设定目标是确定小组活动要把问题解决到什么程度。也是为检查活动的效果提供依据。
注意的是目标要与问题相对应、目标值要量化明确表示、要说明制定目标依据。少数课题特别是管理型的课题很难将目标值量化,这时候应该从其他角度对目标值进行确定,因为量化的目标值在效果检查中容易进行类比,可以更好的说明小组活动成果所达到成效。
在此阶段要描述现状与目标之间的差距如何,体现出可行性分析。
4、分析原因
在现状调查的基础上,全面分析问题(即课题),通过“5M1E”即人(Man)、机器(Machine)、材料(Material)、方法(Method)、环境(Environment)、测量(Measure),对过程进行深入的原因分析,常常恰当地应用质量管理中统计方法工具,如因果图(也叫鱼骨图、鱼刺图)、系统图与关联图,做到图文并茂。在原因分析中一定要全面,将可能的情况全部列出,并分析到每一个末端因素。
5、确定主要原因
确定主要原因(要因)有时可以和分析原因合并进行,也可以分开。确定主要原因就是把因果图、系统图或关联图中的未端因素收集起来,逐条确认排除,以找出真正影响问题的主要因素,也就是罪魁祸首。
要因确定过程不能过于简单。优秀QC小组成果材料在这个环节都做得比较详细,有大量的统计数据和试验来说明。在主要原因确定过程中不能说只是小组成员统一讨论而得出,在分析原因时应注意:首先针对每条需确认的原因要有定量标准,然后通过现场调查用数据对比来证实,再用相应的标准进行比较、对照。
例如:“操作方法不正确、操作不熟练”等,用什么方法检查的,进行了哪些方面的确认工作,结果究竟如何,和有关标准比较来肯定或否定主要原因的存在与否。只有这样,判定的主要原因才依据充分。若没有相应的标准则应在有现场调查验证的前提下,小组成员分析出它可能产生的后果,才能确定它是否是主要原因。
6、制定对策
按照“5W2H”方法即Why(目标)、What(对策)、Who(执行者)、When(时间)、Where(地点)、How(措施方法)、How much(价值),缺一不可,这样制定的对策表才会表现出实效性。
注意对策表中的负责人应与前面确定要因的验证人和后面具体实施的负责人相对应。在记录时间中不要与前面确定要因和后面具体实施的时间发生冲突。
7、实施对策
对策制定完毕,小组成员应严格按照对策表列出的改进措施计划加以实施。在实施的过程中应做好活动记录,把每条对策的具体实施时间、参加人员、活动地点与具体怎么做的,遇到什么困难,如何克服的,花了多少费用都加以记录,以便为最后整理成果报告提供依据。
8、检查效果
把对策实施后的数据与实施前的现状以及小组制定的目标进行比较(要按照PDCA循环方法进行,如果未能达到目标值,小组应进一步分析原因或从现状调查开始再进行新的一轮PDCA循环)。在进行效果对比时,使用的质量管理统计方法/工具应与现状调查时相同为宜。而且,在计算经济效益(实事求是,不可夸大)指活动期间包括巩固期二至三个月。
9、制定巩固措施
对策表中通过实施已证明了的有效措施(如变更的工作方法、操作标准;变更的有关参数、图纸、资料、规章制度等)经过审批后纳入有关的管理文件或制度中,使措施巩固到位。
10、总结及今后打算
成果完成后,小组成员要在一起围绕此次活动进行成败得失的经验分享。
3、8D工具及其应用
在质量管理领域常常会使用8D工具来进行不明原因质量问题的缺陷分析,从众多因素中找出产生质量问题的真正原因,达到改善和提升质量的目的。
那么,什么是8D?8D就是进行质量改善活动解决问题的八个阶段或步骤,又称团队导向问题解决步骤,如图2所示。它是美国福特汽车所发展出来的方法,成立专案项目小组,透过团队合作,用以分析与改善制程能力和客户抱怨,从而达成顾客满意。我国从20世纪90年代中期开始引进并使用8D解决方法,对各企业一些常年累月的、反复出现的质量问题的解决具有很好效果。
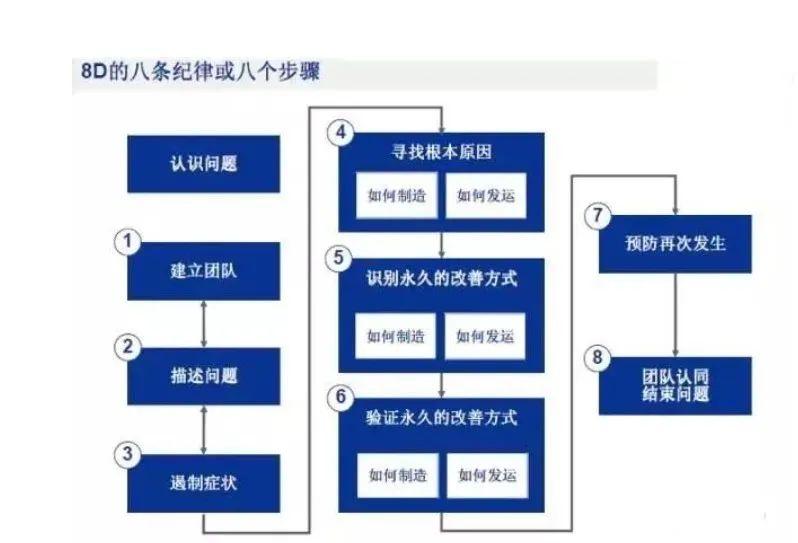
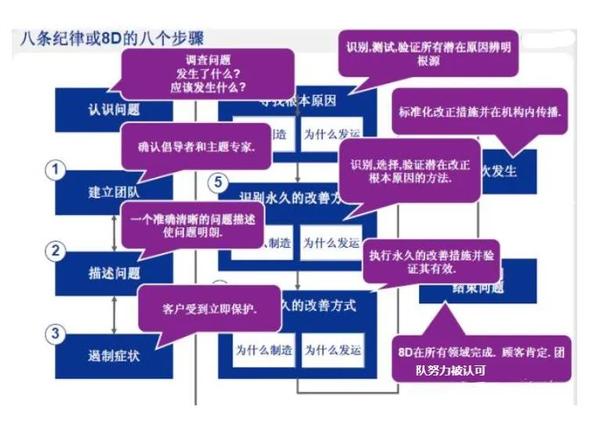
8D全过程示意图
1、成立活动小组1D
当制程中产品偏离预期的质量水平时,建立一个3~10名跨部门的有产品知识、分配时间、职责和技能等需求的技术项目的团队以解决质量问题。
2、掌握现状2D
尽可能多的收集质量问题的信息,使用5W2H(谁、什么、什么时候、哪里、为什么、怎么样、多少)方法,从5M1E(人员、机器、方法、材料、环境、测量)过程因素来可量化的明确记述产品给内外部顾客造成的问题点。问题描述的越详细越完整,对于分析根本原因和解决问题措施的提出越有效。
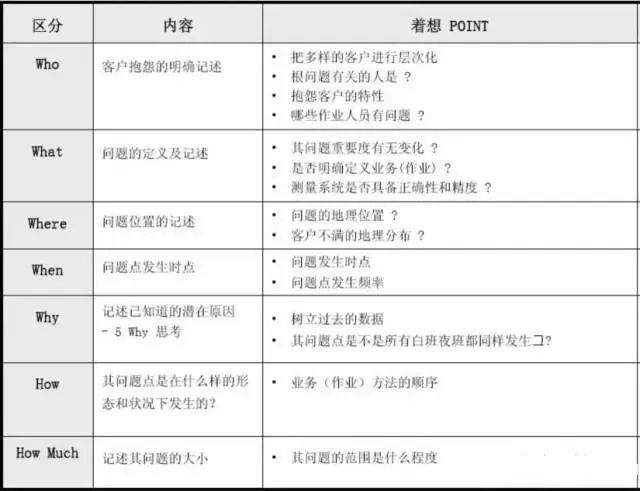
3、实施临时措施3D
在进行根本原因分析和对策之前必须先制定一个或多个临时措施,把质量问题的影响从内外部顾客处隔离, 不让其再发生,即设定执行有效的封锁/围堵措施,动作要快、考虑要全
4、分析根本原因4D
这个阶段最为重要,通过调查、分析和验证说明“为什么会发生、为什么会流出”的所有潜在原因,可以使用象因果图(也称鱼刺图)、排列图、调查表多种形式。只有全面的考虑,找到根本原因,才能为后续的根本对策和有效措施奠定坚实的基础。
5、验证对策方案5D
对于分析出的根本原因是真还是假需经过验证,即通过设定改善目标, 站在顾客的立场实施提出的几个对策,系统的统计证明所提出的对策方案解决问题的结果(包括正向效果和副作用、经济性等)。如果所有的对策都不能达到目标,就说明分析的根本原因欠缺,需要按照PDCA重新进行4.4和4.5,直到找到根本对策。
6、实施根本对策6D
通过验证对策方案的有效性,找到根本对策在产线的产品生产过程中实施,并设定持续的管理方法来确认长期的效果。如果效果不充分,就需要再按照PDCA重新进行4.4、4.5和4.6,直到达到长期稳定的效果为止。
7、防止复发的预防措施7D
质量管理的重点就在于未雨绸缪,预防措施的落实。为了预防问题的复发和其他类似问题点的出现,制定或修编完善质量管理体系和标准(规定及规格)以及指导作业文件、管理新的管理方法或检测点,并及时有效培训。
8、活动评价8D
质量问题的解决,整个团队要进行成果的分享和评价,并对活动的各阶段所得到的数据、分析内容、过程结果等记录。遗留问题是什么,往后怎么解决?然后宣布关闭此8D,解散8D小组。
综上所述,图3给出了8D工具的PDCA循环过程图。无论是试产时发现的质量问题或是量产的客诉问题,公司若依照 8D 工具来解决都是卓有成效的。
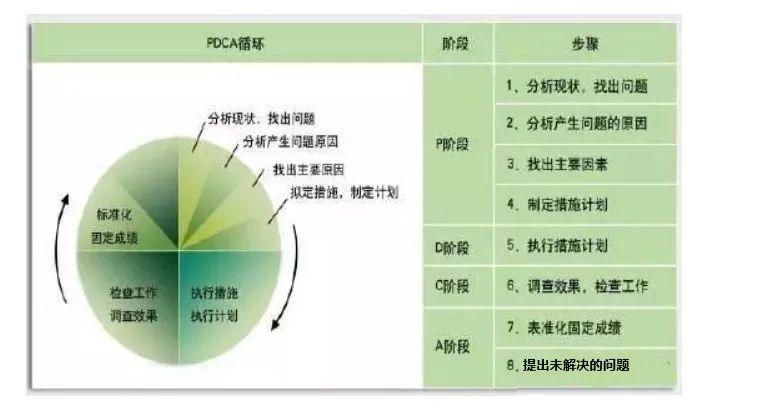
8D方式的PCDA循环图
4、8D工具及其应用
1、都属于质量管理整体构架中的质量改进范畴;
2、都遵循戴明PDCA循环规律;
3、都是团队解决问题:
只不过QC偏向于生产现场解决一个具体小质量问题,多以工人为主组建。8D偏向于一个未知原因的质量问题解决,多以技术、管理人员为主组建,而且须有一个一定权限的头来协调公司必要的资源和支持。
4、步骤大体相同,具有相通性:
都有对质量问题现状的描述或调查、设定目标、分析原因和确定根本原因、效果跟踪验证、形成固化文件指导生产、成果分享的主要过程。
5、都需要一段时间的实践验证,以确保解决问题的有效性。
5、结束语
在很多企业批量生产的流水线上,都建立了严格的工艺规范和操作规程,这些规范和规程在很大程度上提高了工作效率,保证了产品的质量。但随着企业的顾客的变化及产品要求的变化,原来的产品设计开发、工艺技术、工艺规范、工艺流程等势必要发生相应的改变,也会在生产过程出现5M1E因素的变化。
这些改变很有可能引起一些质量问题,这就需要从质量管理的角度予以解决,QC强调“小、实、活、新”,注重身边问题的解决适合于基层生产线上的工序或操作的不合理的质量改进活动。
8D更加专业性,是对棘手的、重复发生的、影响范畴广的、顾客抱怨的问题的质量改进活动。
QC与8D的最大的不同是8D关闭前需要对潜在的类似问题采取预防措施,而QC小组活动末期制定对策并实施后,只有巩固措施及下一部打算,未能对问题的再发生以及相似问题的出现采取有效的预防控制措施。
值得注意的是,企业要进行QC成果和8D成果的分享与发布,进行适当的奖励,形成一种企业质量管理的全员参与的文化,使得在企业的任何岗位都有改进的机会,最大限度地挖掘人的潜力,预防质量问题和持续改进质量,从而提高企业管理水平、降低成本、创造效益和提高顾客满意度。