一、什么是FMEA
FMEA:潜在失效模式与效应分析,全称Potential Failure mode and effects analysis 。最早是由美国国家宇航局(NASA)形成的一套分析模式,FMEA是一种实用的解决问题的方法,可适用于许多工程领域,世界许多汽车生产商和电子制造服务商(EMS)都已经采用这种模式进行设计和生产过程管理和监控。FMEA是一种试错的思维模式,可以理解为给一个清单,告诉可能会犯的错,以及错误的结果和严重性。当面对一个陌生的概念或领域时,有个东西,用来引导,消除陌生,避免因此可能导致的问题发生。这个东西就是FMEA。
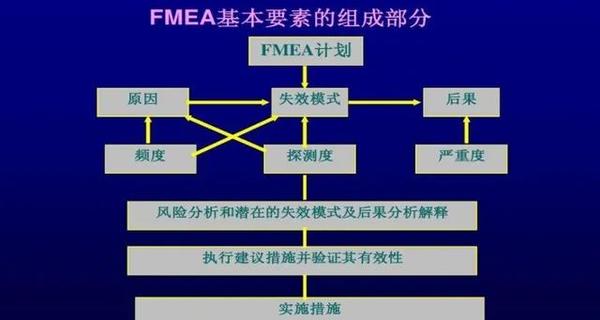
二、FMEA的分类
FMEA通常分为三类:
1.SFMEA(系统失效模式及后果分析):1.将研究的系统结构化,并分成系统单元,说明各单元间的功能关系。2.从已描述的功能中导出每一系统单元的可想象的失效功能(潜在缺陷)。3.确定不同系统单元失效功能间的逻辑关系,以便能在系统FMEA中分析潜在的缺陷、缺陷后果和缺陷原因
2.DFMEA(设计失效模式及后果分析):在设计和制造产品时,FMEA是一种可靠性设计的重要方法。它实际上是FMA(故障模式分析)和FEA(故障影响分析)的组合。它对各种可能的风险进行评价、分析,以便在现有技术的基础上消除这些风险或将这些风险减小到可接受的水平。及时性是成功实施FMEA的最重要因素之一,它是一个“事前的行为”,而不是“事后的行为”。
3.PFMEA(过程失效模式及后果分析):是由负责制造/装配的工程师/小组主要采用的一种分析技术,用以最大限度地保证各种潜在的失效模式及其相关的起因/机理已得到充分的考虑和论述。
三、FMEA分析流程
FMEA分析七步法:
步骤一:策划和准备(定义范围,使用了“5T's 、框图、过程框图”等来定义范围)
步骤二:结构分析(结构分析,使用了“边界图、结构树”等来进行结构分析)
步骤三:功能分析(使用了“P图、功能树、功能矩阵图”等来进行功能分析)
步骤四:失效分析(使用了“FE-FM-FC表、失效网图”等进行失效分析)
步骤五:风险分析(全新的严重度、频度、探测度评分标准,取消了RPN,采用AP优先级)
步骤六:优化(确定降低风险的措施、职责、期限,及措施后的风险再评估)
步骤七:结果文件化(完成FMEA文件,向管理层、客户、供应商沟通风险)
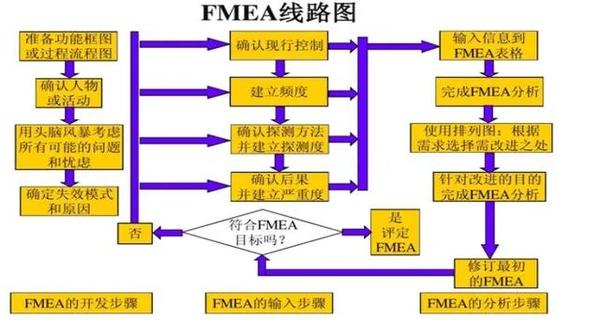
四、FMEA在设备中的应用
FMEA在设备管理中,可以进行设备故障风险预防,保障设备运行的可靠性。
1、用于设备维护计划。制造工厂中设备维护计划(EMP)的主要目的是最小化计划外事件对安全,环境和业务盈利能力的影响。FMEA是实现和维持EMP目标的可靠工具。最佳的长期拥有成本通常是有效促进和彻底实施的FMEA的结果。
2、用于设备失效分析。针对设备运行过程及设备停机状态中的失效模式进行分析,确定失效后果,失效原因,预防、探测手段,然后制定改善措施。
3、用于设备设计。采取科学合理的应用流程和方式来完善设备的实际设计,保证设备的质量,避免设备在实际的使用中出现各种问题。