物料管理是将管理功能导入企业产销活动过程中,为使物料运作有章可依、有依可循,杜绝运作中物料漏洞,严格控制浪费,合理利用物料,有效节约成本。
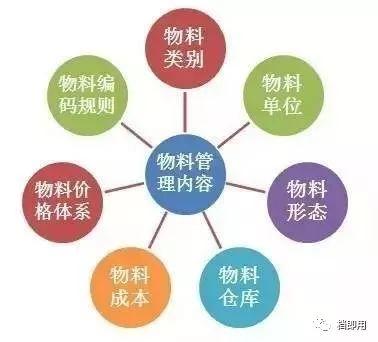
1、物料控制的精髓是“三不”
(1)不断料、呆料:不会让生产线停工等待所需的物料;
(2)不呆料、滞料:需要使用、可以使用的物料购进来,不要让不需要使用、不可以使用的物料进入货仓或呆在货仓不动;
(3)不囤料、积料:物料购入要适时,贮存数量要适量,以减少资金的积压。
2、物料管理8大死穴
追加料处理;
紧急用料处理;
备用料处理;
生产后散料进仓处理;
物料拆lot后处理;
仓库主管现场感不足;
仓管员与成本概念;
废料、品处理;
3、物料库存量管理—安全存量/最高存量/最低存量
适当的库存量管理是物料仓储管理所要实现的目标之一。由于物料的长期搁置,占用了大量的流动资金,实际上造成了自身价值的损失。因此,正常情况下企业应该维持多少库存量也是物料仓储管理重点关心的问题。一般来说,在确保生产所需物料量的前提下,库存量越少越合理。
(1)安全存量
安全存量也叫做缓冲存量,这个存量一般不为平时所用,安全存量只用于紧急备用的用途。
①首先决定各料品的订购点及订购批量标准。
②再运用账务手段随时查核,如发现库存量已低于订购心点,立即订购已设定的定量料品。
安全存量 = 紧急订货所需天数 × 每天使用量
(2)最高存量
最高存量是指生产高峰固定时期内,某项物料(如通用标准物料)允许库存的最高存量。
最高存量 = 一个生产周期的天数 × 每天使用量 + 安全存量
(3)最低存量
最低存量是指生产淡季固定时期内,能确保配合生产所需的物料库存数量的最低界限。
最低存量 = 购备时间 x 每天使用量 + 安全存量
(4)定量库存控制方法
①定量库存控制运用双堆法、三堆法可以达到简便可行的目的。
②双堆法:将订购点物资数量从物资库存中分出来单独存放。当库存量降低已订购点那一堆时,即提出订单订购。
③三堆法:在双堆的基础上,将保险储备的数量又分出一堆,就是三堆法了。
④双堆法和三堆法无需盘点和持续记录,方法很直观。确实简便可行。
⑤定量库存控制法一般适用于价值相对较低用途固定,订购时间较短的物资,对ABC法中的B类物资适用度大。
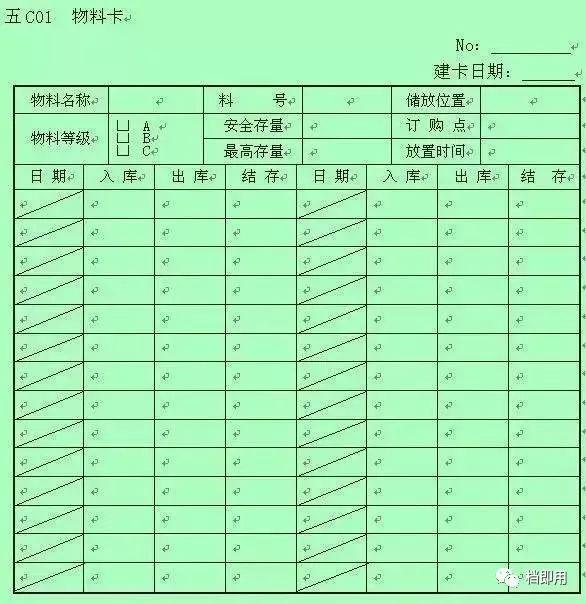
4、10种物料成本降低途径和操作方法:
① 产品的设计
② 材料、零部件的标准化
③ 交期的长短
④ 物料价格
⑤ 库存量的大小
⑥ ABC物料分析法的利用
⑦ 进料的品质
⑧ 搬运和包装的费用
⑨ 管理办法与流程的简洁化
⑩ 呆废料的预防与处理工作
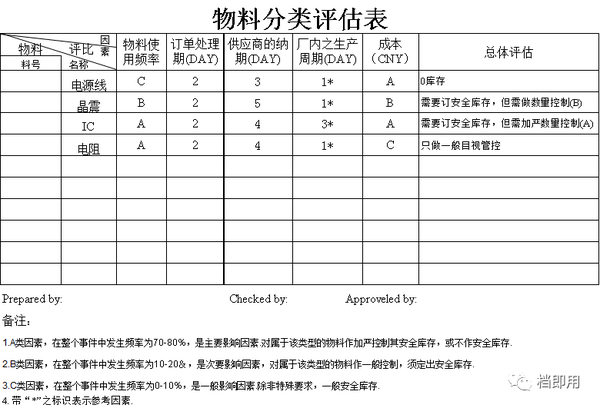
5、存量管制是企业物料管理的核心
(1)存量管制的意义:
存量管制---指以最佳方法控制原料、产品、零件、工具及办公用品的种类与数量;一方面配合企业内各种生产的需要,另一方面使产品保持最低的物料成本。
A、确保生产所需的存量→何时采购,经济订购量多少
B、设立存量管制的基准 →维持适当的存量→供应企业的生产
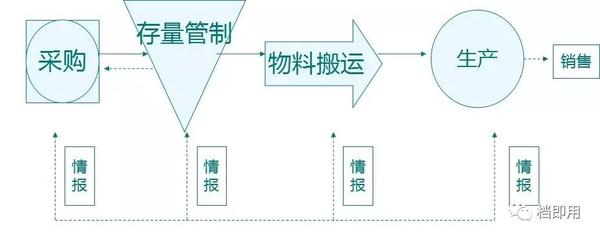
(2)存量管制的八大功效:
不断产
减少物料备购时间
简化运作
方便紧急定单
协调供应商
降低采购成本(价格)
控制容易
减少采购和运输成本
(3)六种情况下存量管制订购:
存货型生产
少品种多批量经常性的物料
共用性多的物料
大宗的物料购备时间长
供应源与使用工厂距离远
『ABC管理法』之C类或B类物料
6、安全库存的设定
影响安全库存的三大因素:
(1)需求的不确定性影响安全库存。需求变动越大,安全库存需要越多;
(2)供应的不确定性影响安全库存。供应越不确定,安全库存需要越多;(3)有货率(服务水平)的要求影响安全库存。服务水平要求越高,安全库存越多。
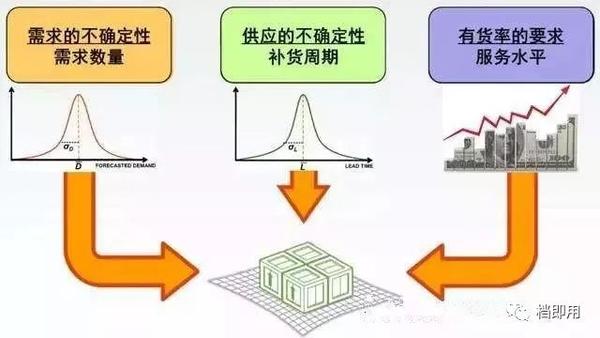
安全库存设定的四大措施:
(1)正本清源:预测越准,意外需求发生的可能性就越小;
需求的预测:行销
制程的品质:制造/品管/工程
供应商的产能:采购、工程、品管、生管
供应商的品质:采购、工程、品管
供应商的交货时间:采购、生管
(2)缩短订货周期与生产周期:这一周期越短,在该期间内发生意外的可能性也越小;
(3)减少供应的不稳定性:其中途径之一是让供应商了解你的生产计划,以便它们能够及早作出安排。另一种途径是改善现场管理,减少废品或返修品的数量,从而减少由于这种原因造成的不能按时按量供应;
(4)运用统计的手法:通过对前6个月甚至前1年产品需求量的分析,求出标准差后即得出上下浮动点后做出适量的库存。
安全库存对于企业满足一定的客户服务水平是重要的,在企业产品供应上起到缓冲的作用,企业往往根据自身的客户服务水平和库存成本的权衡设置安全库存水平。
而在现实情况下,企业的安全库存往往起不到应有的作用,当市场销售繁荣时,根本就没有库存保证供应,缺货水平很高,而在市场萧条时,安全库存显得多余。