当今被称为“传统生产模式”并非指遥远的“手工作坊“,其实它离我们如此之近,至今任然占据着制造业的主流,成为众多制造企业的”传家宝“。传统生产模式专指在第一次世界大战之后,由H.福特首创、并在1913年的底特律高地公园工厂完整实现,经过通用汽车总裁A.斯隆的不断改进与完善,最终形成了严格的体系并达到了人类制造方式的新境界。被称为”大批量生产Mass Production“
相比较手工艺生产方式,大批量生产体现出无与伦比的巨大优势:模块式工艺布局,作业人员的专业分工越来越细,”技能依赖度“大幅减少;”大规模流水线Line装配“大幅缩短了制造周期、极大地提升了装配产出与效率;”零部件标准化“提升了装配的速度与品质保证能力;”规模效益“得以实现,产品的成本大幅下降、售价也越加亲民
但伴随着人类制造业步入买方市场,特别是“多品种、小批量、快交付、低库存”订单模式的日趋主导,“大鱼吃小鱼”的规模竞争已经渐弱、“快鱼吃慢鱼”的速度竞争成为关键,传统的大批量制造模式凸显出严重的缺陷:由于采用模块式生产方式,每个工序间必须批量(Batch)传递,而非一个工件流动,工序间存在大量的加工品、半成品,故WIP多;模块式生产方式由于形式决定了批量生产数量,故T/T(节拍时间)大于C/T(周期时间),L/T(交货周期)长;模块式生产方式由于是工序间批量传递,故可能产生批量不良影响整个工作品质;模块式生产方式根本上就是推动式生产方式,需要大批量生产,结果会产生库存以及搬运浪费。对传统生产模式的突破与革新势在必行!
丰田正是清晰地认识到传统的大批量制造模式的缺陷,在大野耐一的领导之下经过多年的摸索与时间,从宏观角度来看,最终创建了“单件流One Piece Flow”,它成为丰田两大支柱之一“准时化制造Just In Time”的基础。同时从微观角度来看,“线体小型化”成为主流及革新的方向,并最终催生了“细胞化单元生产Cell”
一、大规模流水线Line装配模式的衰落
1、Line装配曾经的辉煌
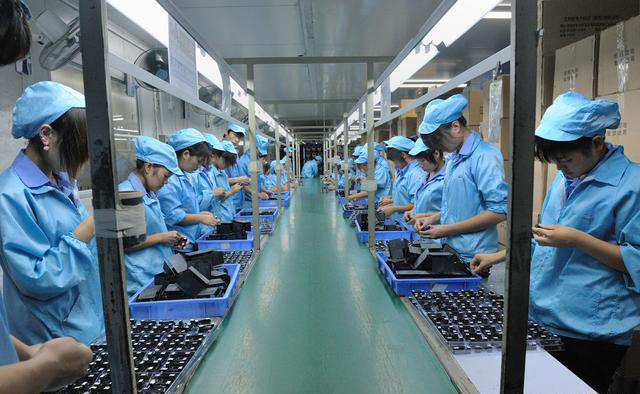
- 模块式工艺布局,作业人员的专业分工越来越细
- ”技能依赖度“大幅减少
- ”大规模流水线Line装配“大幅缩短了制造周期
- 极大地提升了装配产出与效率
- ”零部件标准化“提升了装配的速度与品质保证能力
- ”规模效益“得以实现,产品的成本大幅下降、售价也越加亲民
2、Line装配的致命缺陷
- 如遇机种切换必须等到所有工序全部完成才能切换
- 生产线上所有的部品、半成品以及成品必须完全清除
- 生产线上所有的相关工艺资料、作业指导书、样品以及限度样品必须更换
- 生产线上所有的专用设备、治工具以及辅助工具必须更换
- 频繁的机种切换将导致巨大的“切换工时损失”
二、革新势在必行
1、日本吹响了号角
- 上世纪80年代是日本企业的全盛期,世界500强中日企占了三分之一以上,可是,进入90年代以后,随着“泡沫经济”的崩溃,一家又一家大企业犹如多米诺骨牌似地破产,整个产业界处于一种惊恐失措和信心动摇的状态。于是,一些头脑清醒的企业家开始对过去的做法进行反省,无论是经营战略还是生产方式,也就是对以往被国内外推崇的日本式经营管理进行开刀,以便尽快摆脱困境,重整旗鼓。这时,一位名叫山田日登志的管理咨询专家开始受到关注
- 山田日登志毕业于南山大学法语系,先是当报社记者,后又在歧阜县生产性本部工作,主要是为当地企业开展经营管理方面的咨询,这期间,他认识了丰田公司副总经理大野耐一,被后者讲授的“丰田生产方式”所吸引,便拜大野耐一为师,从头开始学习。1978年,初具实力的山田日登志创办了PEC产业教育中心,走上了职业咨询师的道路。开始他的主要工作是推广“丰田生产方式”,也积累了一些经验。但是,当一些企业反映咨询后的效果不明显时,他也感到内疚,便琢磨起其中的原因来。日复一日,年复一年,山田日登志对流水线本身产生了疑问,即一般企业是否真的需要流水线?流水线有哪些长处和短处?当他带着这些疑问再去企业考察时,发现问题越来越多。那么,山田日登志发现流水线存在哪些问题呢?可以归纳为“4大缺陷”
- 第一,流水线是物质匮缺时代的产物,适合单品种大量生产,但是,当物质生活达到相当高的水准,消费者开始告别大众化的产品而追求个性化的产品时,流水线生产就不适合多品种小批量生产的需要,启动流水线的结果必然导致过剩生产和产品的大量积压
- 第二,以传送带为主的流水线生产的前提是工人的熟练程度和身体情况都相同,能和传送带保持同样的速度,那就能达到最大的效果,也就是说不认可个人之间的差异,但事实上这是不现实的。有的人动作快,有的人动作慢,快的人干完一件活,后面的人还没有干完的话,就只能干等着。而对动作慢的人来说,一件活还没干完,下一件活又传过来了,只能将它拿下来放在一边,等全部干完了再补上。于是,在干得快的人和干得慢的人之间就出现了一些尚未完工的部件,8小时下来,流水线两边滞留的部件多得像小山,而要消化这些小山,要么是加班,要么留到第二天。前者公司要承担加班费,后者等于没有完成当天的生产任务。而且,这些小山究竟意味着什么呢?适时生产的特点之一是需要的时候将需要的量送到指定的地方,所以同时解决了零部件库存的问题,即零库存和无仓库管理。但是,滞留在生产线周围的未完工的部件是不是库存呢?山田日登志认为那就是库存,如果不解决这个问题,那就只能说改变了库存的场所,零库存和无仓库管理也就是一句空话
- 第三,过细的分工导致工人只会干自己的活,也就是单面手,不会干他人的活,这样,当某个岗位缺人时,员工之间的调剂就很困难
- 第四,流水线对工作热情高,想比别人干得更出色一点的人来说是一个不可逾越的障碍,因为“木桶理论”在起作用,流水线在向木桶上的短板看齐
- 针对这些问题,山田日登志提出告别流水线。但是,没有流水线以后怎么生产呢?
2、革新步骤一:长线体短缩化
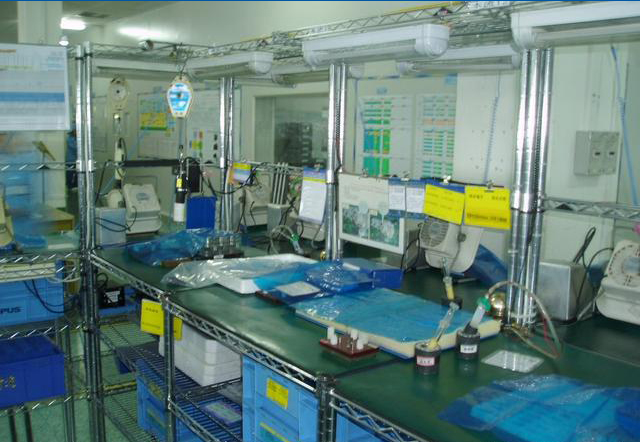
- 取消“运输带”,生产线体由标准作业台组合而成,便于生产线工序的增加与缩减
- 三层标准作业台、立体空间充分利用
- 站立作业(小距离走动作业)
- 面向生产线的作业
- 取消传输带,采用人手传递或工装器具传递
- 工序间在线库存0件(单件流)或少件
- 标准作业、非标准作业完全分离(水蜘蛛角色)
3、革新步骤二:员工技能多能化
- 培养多能工、甚至全能工。当大家都成为多面手以后,就开始减少操作工的数量,比如原来需要12人的流水线,减为10人,过一段时间再减去2人,最后是一个人承担所有的活。这话听起来有些悬,开始谁也不相信,但是NEC、三洋、索尼、松下、佳能等日本电器业的代表性企业的实践已经证明这些做法是可行的
4、革新步骤三:单元生产细胞化
- 完全抛弃流水线,将工作台排列成凹字形,上面按装配的次序摆满零部件、工具以及测试仪器。大到洗衣机、复印机,小到手机、MP3,都由一个或几个工人完成装配。由于这种方式把原来的流水线分解成了一个一个单元式细胞,所以被命名为“细胞生产方式Cell”。同时,因为这样的布局很像集市上的露天店,所以俗称“小店式生产方式”
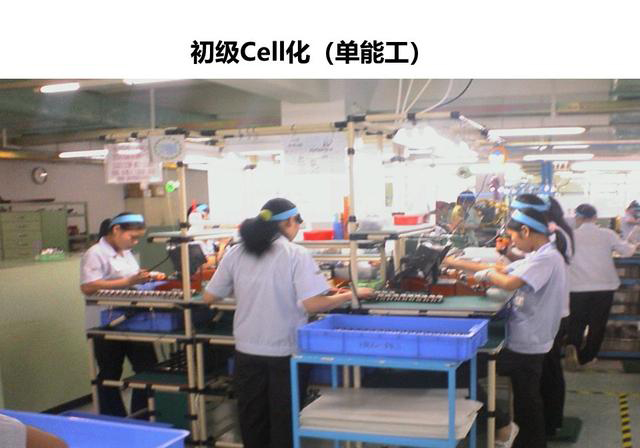
- 当完成了多能工甚至全能工的培养之后,细胞中所需要的作业人员数量便不再固定,而是可以跟据排产计划灵活调配,从而使员工的作业效率得到极大的提高,因此被称为“高级细胞化”
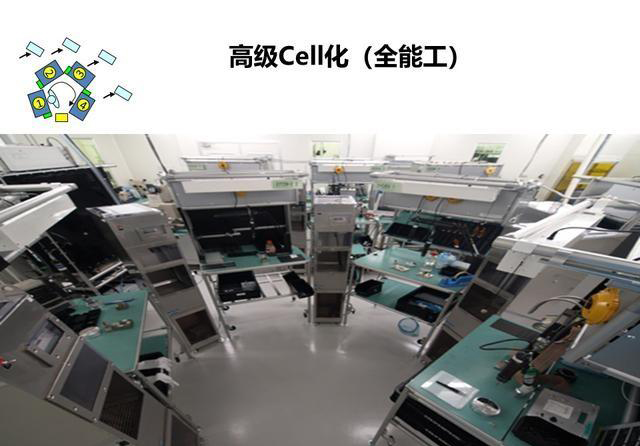
- 为了满足“多批中、小批量、快交付”的生产模式,人类创建了将“细胞化单元生产”与“快速换模SMED”相融合的技术与管理,从而最大程度地减少换模或切换机种带来的产能损失,创建了可以对应全机种混流生产的最新模式,被称为“全能混流式Hybrid”
5、革新步骤四:产线小型化
- 单元生产细胞化的局限在于并不是所有生产线及工序都可以被换成了单元式细胞生产。因为不少工序必须使用共同的设备、机械或传送传输装置,而非人工。以这类工序为对象所产生的就是小型产线。可以说,它的出现是在生产线领域中自单元式细胞生产以来的另一场“革命”
6、单元生产细胞化及小型化的成果
- 空间缩减率飞跃性地提高
- 本田的车身涂装线与以往相比缩短了40%。丰田汽车发动机生产线的设置面积减少了58%。大丰工业的曲轴等发动机轴承生产线与川崎重工业的摩托车生产线的长度减少了一半,电装的铝合金压铸线面积减少了80%。生产线小型化的动向在电机界也迅速发展。例如,在TDK的电源生产线中,装配·检查线的空间缩小了40%
- 以小制大
- 是从制造业以往的“常识”,即越是大量制造就会越便宜的“量产效果”这一想法中脱离出来而形成的。也就是说,它定义为“即便每次生产少量产品,也能控制住制造成本的小规模生产线”。就连在以大规模生产为前提的半导体领域中,小型生产线“Minimum Fab”,即能够把投资费用控制在千分之一的生产线这一划时代的构想也正在变为现实
- 从这种构想中孕育出来的小型线或细胞化会带来很大优势。首先是削减成本(C)。由于生产线自身规模小,而且设置面积也小,所以工厂的建筑物也会缩小。由此,能够控制住投资费用。而且,工序减少,能源费用也会降低,据此能够削减制造成本。
- 小型线对于需求增减的灵活性也很高。即使需求急剧减少,线体也很难成为剩余设备,因为固定费用低,所以易于产生利润。相反,需求急剧增加时,新设线体或增设线体也比较容易进行。最终,这也有利于削减单件产品的成本
- 能够对应突然出现的订货要求
- 依靠导入小型线或细胞化生产而提高的附加价值(V)是指应对种类数量变化的能力的提高。因为能够每次生产少量、有时甚至是一件产品,所以,能够根据必要量来灵活生产不同产品或派生商品、多色产品等不断增加的品种
- 在小型生产线中,速度(S)变快,是因为生产线变短或缩小,相应地就会比以往处理起来更快,生产过程周期时间被缩短了。据此,能够缩短到投入市场为止的时间,所以,易于应对客户突然发出的订货要求,也有利于防止销售机会损失。追踪需求变动的性能的提高,带来了应对种类数量变化的能力的提高
三、单元生产细胞Cell的精密设计
1、利用节拍时间来和客户需求同步
- 节拍时间是能够恰好按时满足客户需求的一种工作速度
- 节拍时间 = 每天净可用时间 / 每天客户需求量
2、一次移动一件
- 上一件作业完毕,下一件作业开始时(理想情况是每个节拍时间)
- 工作流持续无停歇
- 在制品被限制在标准数量
3、基于拉动的作业和移动
- 只有下一个工序‘消耗’时才生产
- 消除过度生产,过剩库存,以及制造错误产品
4、依据工序的顺序设计产线布局
- 为平衡的零件流动创建产品族(PQ分析,零件流程矩阵,加工路线的标准化)
- 避免在单元线里有‘倒流’,尽可能将‘外部工序’纳入到单元线里(或使用SWIP拉动来管理)
5、充分利用U-形线体的优势
6、逆时针流动最合理
- 大多数人使用右手(优势手)的工作效率会更高
- 设备一般都是方便右手操作来设计的
- 右脑习惯性加工由左眼观察到的来自空间的信息
7、明确‘入’和‘出’区域
- 原材料的入口和产成品的出口在同一个点
- 末端动作拉动它的前端动作
- 识别单元的‘入’和‘出’口
- 识别何时货物离开单元线进行线外加工,又何时回到单元线
- 一个工序的出口就是下一个工序的入口——使得物料控制,标准库存和自动传送得以实现
8、将设备间的空间最小化
9、流动无障碍
- 工具箱不要妨碍流动
- 工作凳不可以放在机器前
- 托盘不能放在生产线
10、设备尺寸适当
-
自制工作台,架子和推车
空间正好放得下单件 - 所有设备都有轮子
- 管道和结构连接处非常容易重设
11、设备易于移动
- 可以迅速断开和连接
- 任何设备都有轮子
- 运送零件时,使用手推车,而避免吊车或起重机
- 把设备放置在带刹车的轮子上
- 使用快速连接供电和供气线
12、没有碑柱
-
没有墙,房间或无法移动的牵绊
不要把机器用螺栓锁在地板上
13、易于保养
• 在机器后留3英尺距离作为保养空间
• 允许从后面接近机器(注意在墙与墙之间留有可以接近机器的空间)
• 既要考虑操作员的日常保养,也要考虑设备专业大修所需的空间
14、物料从后部供给
15、考虑安全,人机工程
- 将工位排成一行
- 操作员的移动线要直
- 河流应该没有弯曲
- 线的设计适于零件的自动传送• 将工位排成一行
- 操作员的移动线要直
- 线的设计适于零件的自动传送
16、全体人员要执行标准作业
17、操作员要持有多项技能
18、一个人能够操作整个单元
- 最小化移动和运送的浪费
- 不应有任何任务对独立操作造成困难或危险
- 保持当产线需要增加人手的灵活性
19、最小化走动