6S管理如何让车间效率翻倍?
一、整理(SEIRI)
整理是 6S 管理的起始点,核心在于精准区分必需品和非必需品,坚决清除非必需品。在车间里,积压的原材料、损坏的设备、过期的工具等非必需品大量占用空间,严重阻碍人员与物料的顺畅流动。通过整理,将这些物品清理出去,车间空间得以释放,物料搬运路径大幅缩短,员工能迅速找到所需物品,减少寻找时间,从而显著提升工作效率。
比如,某车间在整理前,员工平均每天花费 30 分钟寻找工具和物料,整理后,这一时间缩短至 5 分钟,每天节省出的大量时间可投入实际生产,效率提升效果立竿见影。
二、整顿(SEITON)
整顿是对整理后的必需品进行科学合理的定位、标识和摆放,全面落实 “三定” 原则,即定品、定位、定量。在车间设置清晰明确的区域标识和物料摆放规则,每种物料和工具都有固定存放位置,并进行醒目标识。员工能瞬间找到所需物品,不仅减少寻找时间,还大幅降低操作失误。
例如,整顿前物料摆放杂乱无章,员工常常拿错物料,整顿后,错误率大幅降低,生产效率随之显著提高。
三、清扫(SEISO)
清扫并非仅仅是表面的打扫卫生,更关键的是及时发现设备和工作环境存在的问题。定期对车间设备、地面、通道等进行全方位清扫,能够敏锐察觉设备潜在故障隐患,如松动的零件、异常的磨损、泄漏等。及时处理这些问题,可有效避免设备突发故障导致的生产中断,有力保证生产的连续性,进而提高生产效率。
比如,某车间通过定期清扫,及时发现并修复设备潜在问题,设备故障率从每月 5 次降至 1 次,有效减少生产停机时间,保障生产高效进行。
四、清洁(SEIKETSU)
清洁是将整理、整顿、清扫工作进行制度化、规范化,形成标准作业流程并严格执行。通过制定详细的清洁标准、工作流程和检查制度,确保车间始终保持整洁、有序的理想状态。稳定的工作环境有助于员工养成良好工作习惯,减少因环境变化导致的效率波动,持续推动生产效率提升。
五、素养(SHITSUKE)
素养是 6S 管理的核心与最终目标,旨在培养员工良好的工作习惯和职业素养。通过培训、宣传和激励等多种方式,让员工深刻理解 6S 管理的意义和重要性,自觉遵守 6S 管理规定。当员工具备良好素养,会主动维护车间整洁、有序,积极参与问题解决和持续改进,从根本上提升车间整体工作效率。
例如,员工养成定期整理工作区域、主动报告设备问题的习惯,车间的工作氛围和效率都会得到显著提升。
六、安全(SECURITY)
安全是 6S 管理新增且极为重要的一环。在车间中,完善的安全管理制度、充足的安全防护设施以及定期的安全培训,能极大降低安全事故发生概率。一旦发生安全事故,不仅会导致人员伤亡,还会使生产被迫中断,造成设备损坏、物料浪费等损失,严重影响生产效率。通过加强安全管理,如设置明显的安全警示标识、定期检查设备安全性能、开展安全应急演练等,可有效预防事故发生。员工在安全的环境中工作,能够更加专注,无需担忧安全问题而分心,从而提高工作效率。
例如,某车间加强安全管理后,安全事故发生率降为零,员工工作效率提升了 20%,同时因避免事故损失节省了大量成本。
综上所述,6S 管理通过整理、整顿、清扫、清洁、素养和安全这六个方面协同作用,从优化工作环境、规范员工行为、保障生产安全等多维度入手,为车间效率翻倍提供有力支撑,全面提升车间的生产效率、产品质量和员工工作状态。
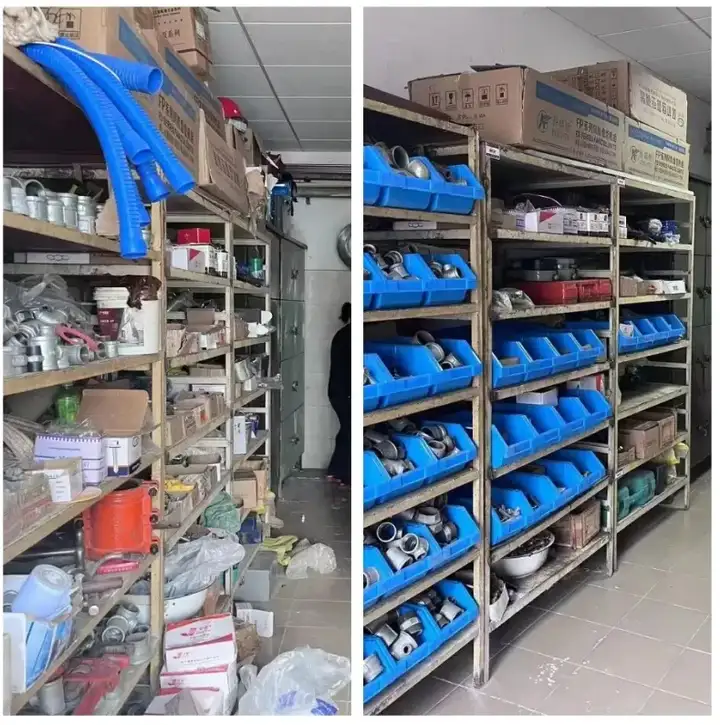
6S 管理在不同行业车间中的应用效果
汽车制造行业:以丰田汽车车间为例
丰田汽车车间全面推行 5S 管理,在整理环节,清理掉生产线旁长期积压的零部件和工具,释放出近 20% 的生产空间,物料搬运距离平均缩短了 30 米。整顿阶段,对各类零部件和工具实施 “三定” 管理,员工寻找所需物品的时间从平均每次 5 分钟缩短至 1 分钟以内,装配效率大幅提升。通过严格的清扫制度,及时发现并解决设备隐患,设备故障率降低了 40%,有效减少了因设备故障导致的停产时间。清洁工作的制度化让车间始终保持最佳状态,员工工作失误率下降了 30%。长期的素养培育,使员工主动参与改进,提出的合理化建议数量增长了 50%,推动生产效率持续提升,产品质量也更加稳定。
电子装配行业:某知名电子企业车间
该电子企业车间在推行 6S 管理后,整理掉大量废旧电子元件和闲置设备,使车间空间利用率提高了 15%。整顿工作规范了电子元件的摆放和取用流程,员工操作失误率降低了 40%,装配效率提高了 35%。清扫过程中,及时发现静电隐患并加以解决,产品不良率从 3% 降至 1.5%。清洁的常态化保障了生产环境的稳定,生产效率波动控制在 5% 以内。员工素养的提升,让团队协作更加顺畅,整体生产效率提升了 40% 以上。
食品加工行业:某大型食品加工厂车间
在食品加工车间,整理环节清理了过期原料和杂物,避免了交叉污染风险,食品安全事故发生率降低了 60%。整顿后,原料和工具摆放有序,生产流程更加顺畅,加工效率提高了 30%。严格的清扫和清洁措施,使车间卫生状况达到更高标准,产品抽检合格率从 85% 提升至 95%。员工素养的提升,使其更加注重食品安全和卫生,主动遵守操作规范,产品质量投诉率下降了 70%,生产效率稳步提升。
通过这些不同行业的案例可以看出,6S 管理在车间中具有广泛的适用性和显著的成效,能够有效提升车间的生产效率、产品质量和员工素养。