引言:传统生产的“冰山式浪费”
在传统制造模式中,企业往往只关注水面上的显性成本(如原材料、人工),却忽视水面下更大的隐性浪费:
-
数据冲击:全球制造业平均有效增值时间仅占生产周期的5%-10%,其余90%以上是等待、搬运、返工等非增值活动;
-
典型案例:某家电企业年营收50亿,但通过精益诊断发现,仅库存积压和过度生产两项,每年吞噬利润超1.2亿。
一、核心理念对比:两种生产模式的本质差异
传统生产模式
-
思维逻辑:推动式生产(Push System)——“先生产再销售”
-
核心特征:
-
大规模批量生产,追求设备利用率最大化
-
部门间各自为政,信息流断裂
-
依赖经验管理,问题解决滞后
精益生产模式
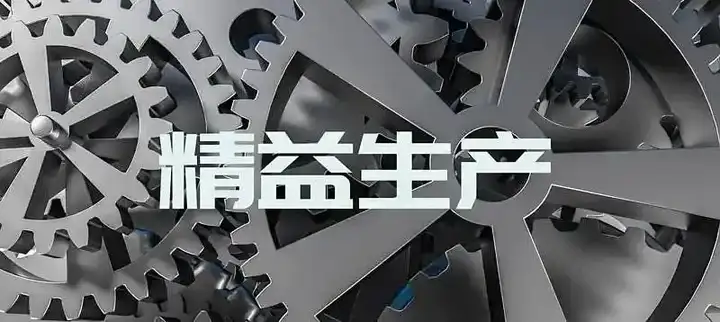
-
思维逻辑:拉动式生产(Pull System)——“只生产客户需要的”
-
核心特征:
-
小批量流动,按节拍时间(Takt Time)精准匹配需求
-
全流程价值流透明化,端到端协同
-
全员参与持续改善(Kaizen)
▼ 关键差异可视化图表
二、成本降低30%的五大维度拆解
1. 库存成本削减:从“资金坟墓”到“流动血液”
-
传统痛点:某机械厂仓库堆满6个月用量的螺栓,占用资金800万
-
精益解法:
-
实施供应商协同JIT(Just In Time)
-
建立超市拉动系统(Kanban),库存周转率提升3倍
-
量化成果:平均库存占用减少45%,释放现金流2600万/年
2. 质量成本归零:从“救火赔偿”到“缺陷预防”
-
传统痛点:汽车零部件厂因漏装垫片,批量召回损失超500万
-
精益工具:
-
防错设计(如扭矩传感器自动报警)
-
自働化(Jidoka)实现“零缺陷流出”
-
量化成果:外部故障成本下降72%,年节省质量成本900万
3. 人工效率提升:从“人海战术”到“人机协同”
-
传统痛点:电子装配线30人日产能1200件,步行浪费占比38%
-
精益改造:
-
U型单元化布局,步行距离缩短65%
-
多能工培训,实现“一人多序”
-
量化成果:人均产出提升2.1倍,人工成本占比从18%降至11%
4. 能源浪费根治:从“粗放消耗”到“精准管控”
-
传统痛点:注塑车间24小时开机,空载能耗占35%
-
精益策略:
-
TPM设备效率分析,识别待机浪费
-
安装智能电表+Andon系统实时监控
-
量化成果:单台设备能耗降低22%,年节省电费超400万
5. 管理成本压缩:从“文山会海”到“现场主义”
-
传统痛点:管理层70%时间用于开会,却无法解决产线断料
-
精益实践:
-
实施Gemba Walk(现场巡查),问题响应速度提升5倍
-
可视化看板替代50%会议
-
量化成果:管理成本占比从12%降至8%,决策周期缩短60%
三、实战案例:某上市公司的精益蜕变
企业背景:国内最大卫浴五金制造商,年产值28亿 改造前:
-
车间在制品堆积高达15天用量
-
月度客户投诉超300起
-
综合毛利率仅19%(行业平均25%)
精益转型路径:
-
价值流分析:锁定冲压车间为突破点,消除37%非增值步骤
-
快速换模(SMED):模具切换时间从85分钟压缩至9分钟
-
拉动系统建设:建立经销商订单直连生产系统的数字看板
成果对比(12个月后):
四、实施路径:四步启动精益革命
-
价值流诊断:
-
绘制当前状态图(Current State Map)
-
计算增值比(Value-Added Ratio)
-
速赢机会挖掘:
-
优先解决“搬运距离最长、库存积压最多”的环节
-
试点突破:
-
选择1条产线进行3个月试点(忌全面铺开)
-
文化固化:
-
建立改善提案制度(每月人均≥0.5条)
-
将精益指标纳入管理层KPI
五、避坑指南:传统企业转型三大误区
-
误区一:重工具轻文化
-
失败案例:某企业花200万买看板系统,却无人更新数据
-
对策:先培养10名内部精益教练
-
误区二:盲目追求自动化
-
失败案例:自动化产线因频繁换型闲置,ROI为负
-
对策:先用精益简化流程,再自动化
-
误区三:忽视供应链协同
-
失败案例:内部效率提升后,因供应商延迟交付再度停产
-
对策:向关键供应商输出精益方法
结语:成本战的终局是价值战
精益生产的本质不是“压榨式降本”,而是通过消除浪费、加速流动、赋能员工,构建持续竞争优势。当传统企业还在为5%的成本削减挣扎时,精益先锋已通过系统性革新实现30%+的成本重构。