一、当优化变成灾难:传统思维的致命陷阱
案例1:汽车厂的“高效”悲剧
某车企为提升产能,投入500万优化焊接车间:
-
焊接速度提升30%
-
机器人利用率达95%
-
结果:车间堆满半成品,月亏损增加200万
问题根源:
喷漆工序(真实瓶颈)最大产能仅支持焊接速度的60%,超速生产导致:
✅ 在制品库存暴增(占用现金流)
✅ 频繁搬运造成车身划痕(质量成本上升)
✅ 喷漆工人被迫三班倒(人力成本激增)
✅ 在制品库存暴增(占用现金流)
✅ 频繁搬运造成车身划痕(质量成本上升)
✅ 喷漆工人被迫三班倒(人力成本激增)
在约束理论(TOC)中,系统产出永远受制于最薄弱环节。优化非瓶颈工序,如同给漏水的木桶加高完好的木板——不仅徒劳,反而加速资源流失。
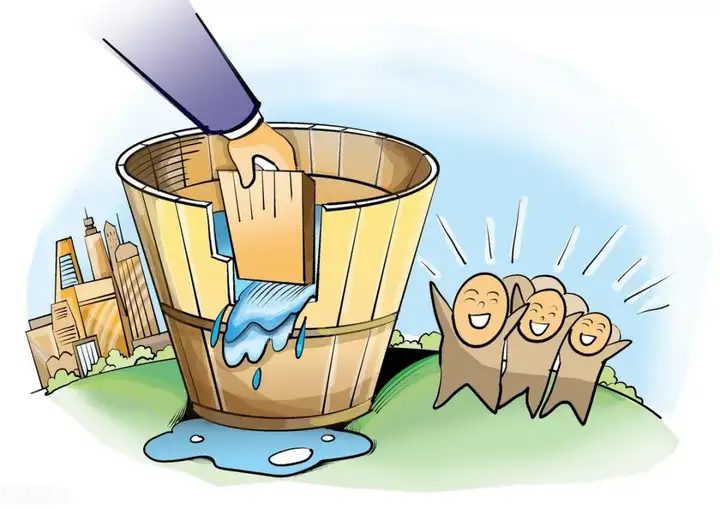
二、识别真瓶颈的三大黄金法则
法则1:寻找“永远饥饿”的工序
食品加工厂实战:
-
包装线频繁停工待料
-
传统思路:斥资200万升级包装机
-
TOC视角:
→ 检测发现杀菌工序是瓶颈(最大产能=包装线需求的80%)
→ 仅花50万增加杀菌釜周转架,整体产出提升25%
识别特征:
-
工序前堆积大量待处理物料
-
设备24小时满负荷运行
-
下游工序经常停工等待
法则2:警惕“伪瓶颈”陷阱
电子厂经典误判:
-
SMT贴片机故障率高(月停机40小时)
-
管理层认定其为瓶颈,计划投资千万更换设备
-
TOC分析显示:
→ 测试工序实际产出仅达贴片机产能的70%
→ 升级测试程序后,全厂产出提升33%
伪瓶颈三大伪装术:
-
局部高负荷(实际不影响系统产出)
-
周期性波动(非持续性制约)
-
人为效率假象(过度加工导致的虚假繁忙)
法则3:绘制动态约束地图
医疗器械厂工具应用:
开发“瓶颈雷达图”,实时监测:
开发“瓶颈雷达图”,实时监测:
-
红色区(当前瓶颈):灭菌仓产能
-
黄色区(潜在瓶颈):原材料检测速度
-
绿色区(非关键点):包装线效率
数据维度:
▸ 工序滞留时间占比
▸ 资源占用强度系数
▸ 下游饥饿指数
▸ 资源占用强度系数
▸ 下游饥饿指数
三、突破瓶颈的“五步爆破法”
医院急诊室的生死时速
初始状态:
-
患者平均等待时间182分钟
-
夜间高峰期死亡率比日间高40%
TOC五步改造:
识别:
-
分诊台是核心瓶颈(处理速度=60人/小时,需求=80人/小时)
榨取:
-
取消非必要登记项(节省30秒/人)
-
设置危重患者直通通道
服从:
-
化验室/药房延长服务至凌晨2点
-
住院部预留5%弹性床位
提升:
-
培训分诊护士使用AI预诊系统
-
增加移动分诊终端
迭代:
-
建立瓶颈动态预警机制
-
每月更新约束地图
成果:
-
平均等待时间降至48分钟
-
夜班死亡率下降55%
-
医护加班时长减少60%
四、构建持续改善的约束管理系统
机制1:缓冲器设计
化工企业实践:
-
在蒸馏塔(瓶颈)前设置2小时原料缓冲库
-
在包装线(非瓶颈)后设置0.5小时成品缓冲
-
效果:
→ 设备故障影响降低70%
→ 订单准时交付率提升至99%
机制2:鼓-缓冲-绳(DBR)控制
汽车零部件厂应用:
-
鼓:按喷漆工序(瓶颈)节拍安排生产计划
-
缓冲:在喷漆工序前设置4小时物料缓冲
-
绳:通过信息系统反向控制原材料投放
-
收益:
→ 在制品库存减少65%
→ 生产周期缩短40%
五、TOC思维的跨界启示
启示1:个人时间管理
-
识别瓶颈:找出限制职业发展的关键能力(如英语/编程)
-
聚焦突破:将70%学习时间投入瓶颈领域
-
案例:
某工程师用6个月专攻Python自动化,薪资涨幅超同期全面学习者
启示2:商业战略制定
-
餐饮连锁店改造:
原瓶颈:中央厨房产能 → 改为前置仓模式后,新瓶颈变为门店服务速度 -
战略价值:
通过转移瓶颈实现商业模式升级
结语:让管理回归本质
TOC的终极智慧:
-
不要试图让所有环节都做到90分
-
确保瓶颈环节达到95分,其他环节60分足矣
-
真正的效率提升,始于对系统约束的敬畏
当你的企业出现这些信号,说明正在错误优化:
???? 某个工序永远“吃不饱”
????仓库堆满上游工序的半成品
????高管热衷于给非瓶颈部门颁奖
▌ 你的瓶颈雷达启动了吗?
① 本周观察:哪个工序的物料堆积最严重?
② 立即行动:用“五步爆破法”发起突击战
③ 长期机制:建立动态约束监控仪表盘
① 本周观察:哪个工序的物料堆积最严重?
② 立即行动:用“五步爆破法”发起突击战
③ 长期机制:建立动态约束监控仪表盘