当特斯拉上海超级工厂实现从钢板到整车下线仅需45小时的制造速度,当丰田九州工厂每百台车质检问题数仅为行业平均值的1/8,这些数字背后都指向同一个底层逻辑——精益生产的系统化实践。
本文深度解析全球五大汽车巨头的精益转型路径,揭示传统制造业突破成本困局、实现价值跃迁的实战方法论。
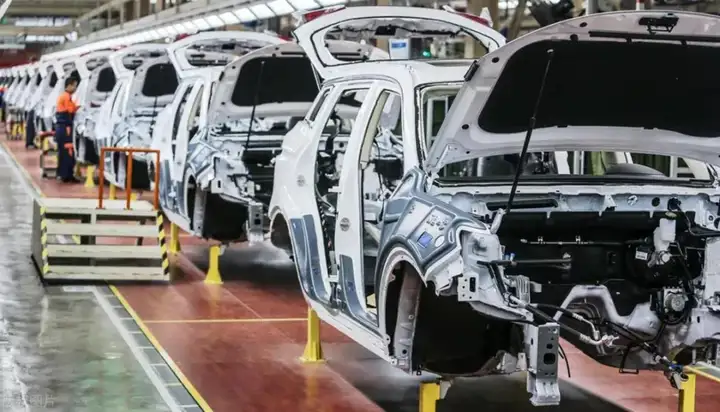
一、丰田TPS进化论:从消除浪费到创造价值流
九州宫田工厂的零缺陷革命 作为雷克萨斯核心生产基地,该工厂将传统七大浪费扩展至"第8大浪费——知识浪费",构建三层防御体系:
-
工序级防错:发动机装配线配置267个传感器,实时监测螺栓扭矩、密封胶厚度等23项参数
-
系统级拦截:通过MES系统比对工序履历,发现未执行检测工序自动锁止移载机
-
组织级保障:建立"质量道场"培训体系,新员工需完成200小时缺陷情景模拟训练
成果:整车Audit评审分值提升至98.7分,质量成本占比降至0.8%(行业平均2.3%)
供应链协同创新 开发供应商协同平台(SCP),实现:
-
零部件库存周转率从15次/年提升至36次
-
模具切换时间通过共享设备利用率数据降低42%
-
建立成本透明化的"价值工程联盟",年度降本达采购额3.2%
二、大众MQB平台的模块化奇迹
平台化生产的成本重构 通过模块化横向矩阵设计,大众实现:
-
开发成本降低20%,零件通用率提升至70%
-
产线切换时间从56小时压缩至8小时
-
单台制造成本下降€1200
沃尔夫斯堡工厂的数字化精益
-
应用数字孪生技术模拟生产线,设备布局效率提升19%
-
AGV物流系统与生产节拍实时联动,在制品库存降低63%
-
工人佩戴AR眼镜指导复杂装配,培训周期缩短75%
三、特斯拉的一体化压铸技术革命
上海超级工厂的成本颠覆 采用6000吨级Giga Press压铸机:
-
将70个零件整合为1个整体铸件,焊接点从800个减至50个
-
车身产线长度缩短35%,厂房面积节省20%
-
单件制造成本降低30%,缺陷率下降40%
生产节拍同步系统
-
电池车间与总装车间通过智能配送系统实现秒级响应
-
采用激光雷达扫描技术,将车身匹配精度控制在±0.1mm
-
建立"问题作战室",异常停线时间缩短至4.3分钟/日
四、吉利汽车的数字化转型路径
春晓基地的智能柔性产线
-
配置217台协作机器人,实现5款车型混流生产
-
通过视觉检测系统自动识别3000种零部件
-
开发工艺大数据平台,将换模时间压缩至行业平均值的1/3
供应链穿透式管理
-
构建四级供应商可视化系统,风险预警提前7天
-
实施VMI库存共享计划,周转率提升至18次/年
-
与宁德时代共建"产能银行",实现电池供应动态调节
五、福特铝车身精益化突破
F-150皮卡生产的价值流再造
-
采用军用级铝合金替代钢材,重量减轻320kg
-
开发电磁冲压技术,将车门板生产工序从8道减至2道
-
建立闭环铝材回收系统,材料利用率达92%
鲁日中心的零距离布局
-
将冲压、焊装、涂装车间直线距离压缩至300米
-
应用数字墨水技术,实现个性化订单实时排产
-
推行"三现主义"(现场/现物/现实),管理层每日4小时现场巡查
(战略级启示)
这些案例揭示汽车行业精益转型的三大趋势:
-
技术穿透:从工业工程向数字工程跃迁,IoT+AI构建实时价值流
-
系统重构:打破组织边界,构建"研发-制造-供应链"一体化作战体系
-
人机共融:将员工智慧转化为算法逻辑,实现持续改善的永动机制
正如丰田生产系统创始人大野耐一所言:"精益不是一套工具,而是培养能发现浪费的眼睛。"当中国新能源汽车渗透率突破40%的今天,精益生产正在从成本控制手段进化为价值创造引擎,这场制造业的"静默革命",将决定未来十年全球汽车产业的竞争格局。