当丰田供应商电装公司通过PDCA循环将某传感器缺陷率从3200PPM降至12PPM,当特斯拉上海工厂运用数字化PDCA将Model Y白车身尺寸公差控制在±0.5mm以内,这些成就揭示:在智能制造时代,PDCA不仅是质量改进工具,更是企业构建持续竞争力的操作系统。
本文通过制造业二十年数据追踪,解码PDCA循环的进化逻辑与实战应用。
一、PDCA的本质重构:从质量工具到战略导航系统
1.1 制造现场的"卫星定位原理" PDCA循环本质是制造业的"动态纠偏系统":
-
Plan(计划):如同输入目标坐标,需包含3D目标设定(质量目标+成本目标+交付目标)
-
Do(执行):相当于路径规划,要求建立过程控制点(如汽车焊装的256个在线检测站)
-
Check(检查):类似GPS实时定位,通过IoT设备每秒采集800+质量参数
-
Action(改进):即自动巡航修正,应用AI算法预测偏差趋势
1.2 数字化转型下的PDCA进化 某变速箱工厂案例显示:
-
传统PDCA周期:45天(人工收集数据→Excel分析→会议决策)
-
数字PDCA周期:6小时(MES系统自动触发改善流程)
核心突破点: -
实时数据流替代抽样检测
-
机器学习替代经验判断
-
自动闭环控制替代人工干预
二、四阶裂变:PDCA在质量改善中的实战演绎
2.1 Plan阶段的"三维透视法" 大众汽车某冲压车间的应用:
-
问题定义:通过质量成本分析锁定占损失63%的表面划伤问题
-
目标设定:SMART原则量化(划伤率≤0.8件/千冲次,3个月内达成)
-
方案设计:5Why分析追溯至模具清洁度不足,制定三级防错方案
2.2 Do阶段的"过程控制金字塔" 特斯拉电池组装线的实践:
-
一级控制:217个视觉传感器实时监控电极对齐度
-
二级控制:SPC系统自动识别过程偏移趋势
-
三级控制:每班次执行过程能力CPK专项验证
2.3 Check阶段的"数据驾驶舱" 某日系车企的数字化检测体系:
-
实时看板:整合设备OEE、直通率、CPK等12项核心指标
-
异常预警:AI算法提前4小时预测质量波动
-
根因分析:自动生成柏拉图/鱼骨图/关联矩阵
2.4 Action阶段的"改善生态链" 博世苏州工厂的创新机制:
-
短期对策:8D报告24小时内闭环简单问题
-
长期对策:QCC小组开展防呆装置开发
-
知识沉淀:将改进方案写入数字作业指导书
-
横向展开:自动推送相似工序改善建议
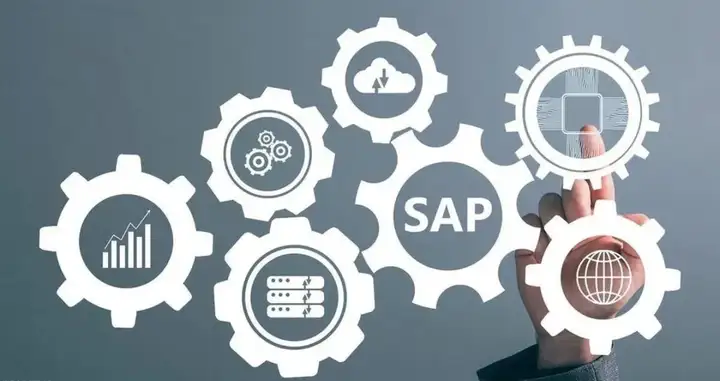
三、突破性应用:PDCA与精益工具的融合创新
3.1 DMAIC+PDCA双循环体系 某发动机工厂的实践路径:
-
Define阶段:用VOC(客户之声)工具锁定关键质量问题
-
Measure阶段:实施MSA(测量系统分析)确保数据可靠性
-
Analyze阶段:通过假设检验定位真因
-
Improve阶段:设计实验验证改善方案
-
Control阶段:建立控制计划固化成果
3.2 丰田A3报告与PDCA的深度耦合 典型A3报告结构演化:
-
问题描述:现地现物拍摄+损失金额量化
-
目标设定:挑战行业标杆水平
-
根因分析:5Why+因果矩阵组合使用
-
对策实施:明确验证方法与责任矩阵
-
效果确认:财务收益与能力提升双重评估
-
标准化:修订3类标准文件(作业/点检/控制)
四、数字化转型下的PDCA新形态
4.1 数字孪生驱动的虚拟PDCA 宝马慕尼黑工厂的实践:
-
在虚拟模型中模拟工艺变更效果
-
预测质量风险并优化控制方案
-
将验证通过的方案直接下发设备
4.2 AI赋能的自主改善系统 案例:海尔互联工厂的"质量大脑"
-
自动识别异常模式(准确率92%)
-
推荐改善对策(采纳率78%)
-
自学习优化算法(每月迭代版本)
五、持续循环的底层逻辑:组织能力建设
5.1 人才培育的三层架构
-
基础层:全员PDCA思维训练(每日5分钟改善日志)
-
专业层:质量工程师掌握高阶工具(实验设计/统计建模)
-
领导层:建立战略部署矩阵(Hoshin Kanri)
5.2 文化变革的四个抓手
-
可视化管理:将PDCA进展投射到车间数字大屏
-
即时激励:扫码提交改善建议即时获取积分
-
失败包容:设立"试错基金"鼓励创新
-
标杆塑造:每月评选"质量改善之星"
(未来展望)
当工业4.0遇见精益生产,PDCA循环正在进化为"智能持续改进系统(i-CIP)"。未来的质量改善将呈现三大趋势:实时化(从月度循环到分钟级迭代)、预见性(从解决问题到预防问题)、自组织(从人工驱动到算法驱动)。
正如质量管理大师朱兰预言:"21世纪的质量战争,本质是组织学习速度的竞争。"在这个时代,掌握PDCA的深度应用能力,就是获得永续改善的基因密码。