开篇案例:一场价值500万的“浪费革命” 2024年,某大型氯碱化工厂因能源成本飙升陷入亏损。管理层调研发现:蒸汽管道保温层破损导致热能浪费20%,反应釜投料误差率高达8%,设备空转时间占生产周期的15%……这些“隐形漏洞”每年吞噬企业500万元利润。
引入精益生产后,该厂通过“三分钟温度巡检法”和“投料精准度擂台赛”,仅用半年就将能耗降低30%,订单交付准时率提升至98%。化工行业的精益转型,不是选择题,而是生存题。
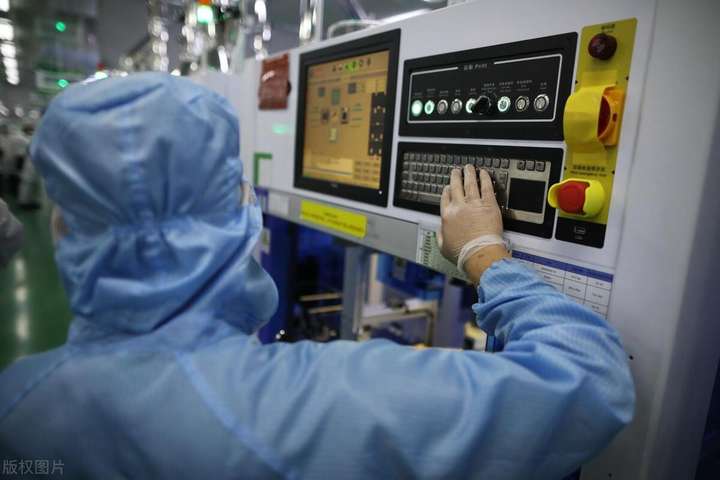
一、化工行业实施精益生产的5大独特挑战
1️⃣ 流程刚性:停不下来的“庞然大物”
化工生产多为连续流程,设备启停成本极高。
-
案例:某乙烯装置紧急停机1小时,直接损失超80万元,重启需72小时恢复工艺平衡。
-
痛点:传统精益的“小批量快速调整”模式在化工场景中水土不服。
2️⃣ 安全与效率的“跷跷板”
化工生产中,过度追求效率可能引发安全风险。
-
反面案例:某农药厂为缩短反应时间,擅自提高反应釜温度,导致有毒气体泄漏(直接损失1200万元+停产整顿3个月)。
3️⃣ 复杂供应链的“蝴蝶效应”
从原油到树脂颗粒,供应链涉及数十种原料、上百家供应商。
-
数据:某涂料企业因助剂供应商延迟交货,导致3条生产线交替停工,月度产能损失达35%。
4️⃣ 数据黑箱:看得见的设备,看不见的浪费
化工过程参数(温度、压力、催化剂活性)的隐性浪费难以量化。
-
典型场景:反应转化率从92%降至89%,肉眼难以察觉,但年损失纯利润超200万元。
5️⃣ 人员惯性:“老师傅”与“新工具”的冲突
二十年工龄的操作工,往往更信赖经验而非数据看板。
-
调研发现:65%的化工企业推行数字化精益工具时,遭遇基层员工隐性抵制。
二、破局之道:4大策略打造“化工精益范式”
策略1:从“硬停机”到“软优化”——柔性精益改造
-
核心方法:
-
在连续流程中嵌入微调单元(如加装在线pH值调节模块,避免整体停机)
-
开发工艺参数动态优化算法(某石化企业通过实时调整裂解深度,将轻油收率提升2.3%)
-
工具推荐:
-
APCD(化工专用价值流图):标记从原料进厂到成品出库的38个关键控制点
策略2:安全为基的“双螺旋改善”
-
实施路径:
-
红线机制:将HAZOP分析(危险与可操作性研究)嵌入每日晨会(案例:某氟化工企业通过HAZOP+5Why分析法,年事故率下降67%)
-
安全可视化:用红/黄/绿三色标注高风险操作区,设置防呆装置(如误操作自动锁停系统)
策略3:供应链的“弹性精益网络”
-
创新实践:
-
供应商协同库存(VMI):某树脂企业与催化剂供应商共享库存数据,紧急补货周期从72小时压缩至8小时
-
数字孪生演练:模拟极端天气/政策变动下的供应链中断场景,制定分级响应预案
-
成效:某上市化企通过构建区域仓储联盟,物流成本降低18%,断供风险下降40%
策略4:用“游戏化”打破组织坚冰
-
激活基层的三板斧:
-
技能图谱积分制:员工掌握SPC(统计过程控制)等工具可兑换培训津贴
-
改善提案擂台赛:某染料厂开展“金点子大赛”,一线员工提出的“离心机节水方案”年省水费50万元
-
师徒制2.0:老师傅带徒解锁数字化工具,同步录制“故障处理短视频”入库
三、长效引擎:化工精益的3个进化方向
-
AI预测性维护:通过振动频谱分析提前14天预警压缩机故障(某甲醇企业故障停机时间减少85%)
-
碳足迹精益管理:将碳排放数据纳入价值流图,识别工艺减碳机会点(案例:某纯碱厂通过余热回收系统,年减碳2.1万吨)
-
产业链级精益协同:组建化工园区共享维修中心,降低中小企业设备管理成本
结语:精益不是一场运动,而是一种生存哲学
当化工行业从规模扩张转向质量竞争,精益生产将成为穿越周期的诺亚方舟。那些在波动中精准控制每个反应釜、每根管道的企业,终将赢得未来。