在当下风云变幻的商业战场中,企业们都在绞尽脑汁,寻觅提升效率、削减成本的秘诀。
精益生产,这一备受推崇的高效生产理念,宛如一盏明灯,照亮了众多企业前行的道路。
然而,你是否知晓,在日常生产流程的 “隐秘角落”,潜藏着诸多不易察觉的浪费,它们恰似潜伏在暗处的 “利润窃贼”,悄无声息地侵蚀着企业的竞争力。
今天,就让我们一同拨开迷雾,深入探寻精益生产中的八大浪费类型,并研究如何将这些 “拦路虎” 逐一清除。
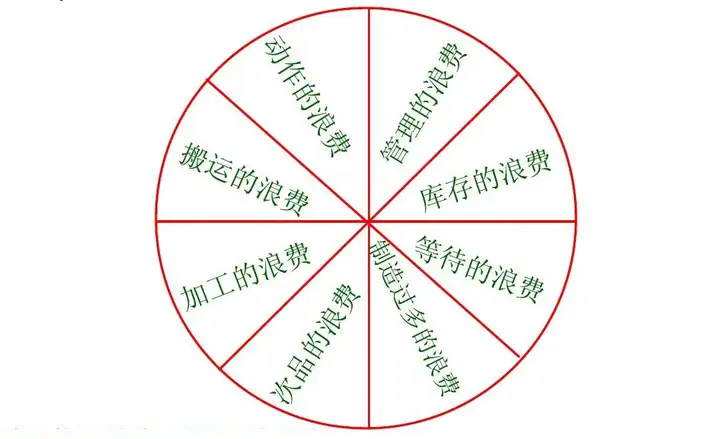
1、过量生产的浪费:囤货如山,得不偿失
过量生产堪称生产界的 “囤货狂魔”。想象一下,有一家服装企业,满心期待着旺季订单如潮水般涌来,于是在淡季便火力全开,疯狂赶制服装。可当旺季的喧嚣渐渐褪去,仓库里却堆积如山,满是滞销的衣物。
这些过剩的库存,不仅占用了大量宝贵资金,还霸占了额外的仓储空间。更为糟糕的是,随着时间的无情流逝,服装款式迅速过时,无奈之下,只能大幅打折促销,甚至直接报废处理,企业损失惨重。
丰田汽车在发展早期,也曾深陷这一困境。彼时,过度生产的汽车积压成灾,资金与场地被大量占用。
后来,丰田果断引入准时化生产(JIT)理念,精准依据客户订单来安排生产,只有在接到订单后,才开始生产相应数量的汽车。这一举措成效显著,成功甩掉了过量生产的沉重包袱,资金周转率大幅提升,如同装上了强劲的动力引擎。
企业若想摆脱过量生产的桎梏,需构建一个精准如 “神算子” 般的需求预测系统,时刻与客户保持紧密沟通,敏锐捕捉市场需求的细微变化。
同时,果断切换至拉动式生产模式,让客户订单成为指挥生产的 “指挥官”,而非仅凭主观臆测盲目生产。
2、等待的浪费:干瞪眼的损失
在生产线上,工人们常常会陷入 “干瞪眼” 的无奈境地。原材料供应不及时,他们只能百无聊赖地等待材料到位,才能继续手头的工作;设备突发故障,维修期间整个生产线瞬间停滞,员工们只能无所事事,白白浪费时间。
有家电子组装厂就深受其扰,供应商送货总是 “慢悠悠”,每个月生产线都会因等待原材料而停工数小时。
这一停工,不仅浪费了工人的宝贵工作时间,还严重打乱了整个生产计划的节奏。后来,该厂与供应商重新 “约法三章”,明确了送货时间,并搭建了库存预警系统,一旦库存低于安全线,便能及时补货。
这一系列举措,成功大幅缩短了生产线的等待时间,生产效率直线攀升。
要消除等待的浪费,企业必须精心优化供应链管理,与供应商建立牢不可破的紧密合作关系,确保原材料按时、按量送达。
同时,强化设备的维护保养工作,制定完备的设备故障应急预案,最大程度缩短设备故障停机时间。此外,合理规划生产流程,杜绝工序之间的衔接不畅,减少等待情况的发生。
3、运输的浪费:冤枉路,冤枉钱
物料和产品在不必要的搬运与运输过程中,同样会造成惊人的浪费。例如,有的工厂布局宛如一座错综复杂的 “迷宫”,原材料从仓库运往生产车间,需历经多个迂回曲折的路线,这不仅耗费大量时间与人力,运输途中物料还极易受损。
某汽车制造企业曾面临这样的难题,工厂内零部件运输距离过长,导致运输成本居高不下,效率却极为低下。
于是,他们痛下决心,对工厂布局进行了大刀阔斧的重新规划,将相关工序和设备紧密安置在一起,零部件的运输路程大幅缩短。同时,引入先进的自动导引车(AGV),实现了物料运输的自动化,运输成本和时间双双大幅降低。
企业可借鉴这家汽车制造企业的经验,对工厂布局来一场彻底的 “大变身”,将生产流程相关环节尽可能靠拢,减少物料搬运的冤枉路。积极采用先进的物流设备和技术,让运输效率实现质的飞跃,降低运输途中的损耗。
4、库存的浪费:囤货的代价
除了过量生产引发的库存积压,不合理的库存管理同样是个 “吞金巨兽”。过多的原材料库存,意味着大量资金被死死占用,而且随着存放时间的增加,库存物资极有可能变质、损坏。
一家食品加工厂,为防止原材料短缺影响生产,大量囤积面粉、糖等原材料。结果,部分原材料因存放时间过久,受潮变质,只能忍痛丢弃。
后来,该厂引入库存管理系统,依据生产计划精准计算原材料需求量和采购时间,将库存维持在合理水平,既有效避免了缺货风险,又显著减少了库存浪费。
企业应运用科学的库存管理方法,比如借助 ABC 分类法对库存物资进行分类管理,重点关注价值高、用量大的物资。同时,与供应商建立高效的快速补货机制,朝着低库存甚至零库存生产的目标稳步迈进。
5、加工的浪费:多此一举的损耗
加工过程中,如果工艺不合理或者过度加工,同样是在白白浪费资源。比如某机械加工厂在生产零件时,采用了极为复杂的加工工艺,虽说能保证零件质量,但耗费的时间和能源多得惊人,生产成本也随之直线上升。
一家家具厂也遇到过类似状况,在木材加工环节,部分工人为确保产品质量,对木材进行过度打磨,远超实际需求标准。这不仅浪费了大量人力和时间,砂纸等耗材的使用量也大幅增加。
后来,该厂对加工工艺进行优化,制定了清晰明确的加工标准和操作规范,工人严格按照标准操作,产品质量得以保证,加工浪费也大幅减少。
企业要定期对生产工艺进行全面评估和优化,剔除不必要的加工步骤,积极采用先进的加工技术和设备,提升加工效率和质量,降低加工成本。
6、动作的浪费:无效忙碌的消耗
在车间里,工人一些不必要的动作也会造成浪费。比如,工人在操作过程中频繁弯腰去拿工具,或是转身寻找物料,这些多余的动作不仅耗费体力,还延长了作业时间。
有一家玩具厂,工人在组装玩具时,工具摆放杂乱无章,每次拿取工具都要花费不少时间寻找。后来,工厂重新设计了工作台,将常用工具按照操作顺序整齐摆放,工人伸手就能拿到所需工具,减少了无效动作,工作效率明显提高。
要消除动作的浪费,企业需要对工作场所进行合理布局,根据操作流程优化工具和物料的摆放位置,让工人能够以最便捷的方式完成工作,减少不必要的动作。同时,开展员工培训,让他们掌握高效的工作动作规范,提高操作效率。
7、不良品的浪费:瑕疵带来的损失
生产过程中出现不良品,意味着之前投入的人力、物力、财力都打了水漂。一家手机组装厂,由于部分零部件质量不过关以及组装工艺问题,生产出了一批有屏幕显示故障的手机。
这些不良品不仅需要返工维修,耗费额外的人力和时间,严重的甚至只能报废处理。后来,该厂加强了对原材料供应商的质量管控,引入先进的检测设备,在生产过程中增加多道质量检测工序,从源头减少不良品的产生,降低了因不良品造成的损失。
企业要建立完善的质量管理体系,从原材料采购、生产过程到成品检验,每一个环节都严格把控质量。加强对员工的质量意识培训,让他们明白质量的重要性,同时采用先进的质量检测技术和设备,及时发现和解决质量问题,减少不良品的浪费。
8、管理的浪费:无序管理的代价
管理不善同样会导致大量浪费。例如,企业内部信息沟通不畅,部门之间协调不到位,就会出现重复工作、决策延误等问题。
一家制造企业,市场部门接到客户订单后,未能及时准确地将订单信息传达给生产部门,导致生产部门按照旧的生产计划进行生产,生产出来的产品不符合客户需求,只能重新生产,造成了极大的浪费。
后来,该企业引入了信息化管理系统,实现了部门之间信息的实时共享和快速传递,同时优化了工作流程,明确了各部门职责,有效减少了管理上的浪费。
企业要建立科学合理的管理制度和流程,明确各部门和岗位的职责,加强信息沟通与协作。利用信息化手段提高管理效率,实现资源的优化配置,避免因管理混乱而产生的浪费。
精益生产中的这八大浪费,如同隐藏在企业内部的 “蛀虫”,持续侵蚀着企业的效益和竞争力。
但只要我们精准识别并全力消除这些浪费,企业便能实现生产效率的飞跃、成本的有效降低,在激烈的市场竞争中脱颖而出。
记住,消除浪费,就是为企业创造价值;减少一分浪费,就多一分企业的未来。让我们携手踏上精益生产的变革征程,为企业铸就辉煌的明天。