在当下竞争白热化的机械加工行业,成本居高不下、生产效率低下、产品质量参差不齐等难题,像一座座大山,压得众多企业喘不过气。
不过,有不少企业另辟蹊径,通过精益生产转型,成功突破困境,实现华丽转身。今天,咱们就一起来探究机械加工企业的精益生产转型之路。
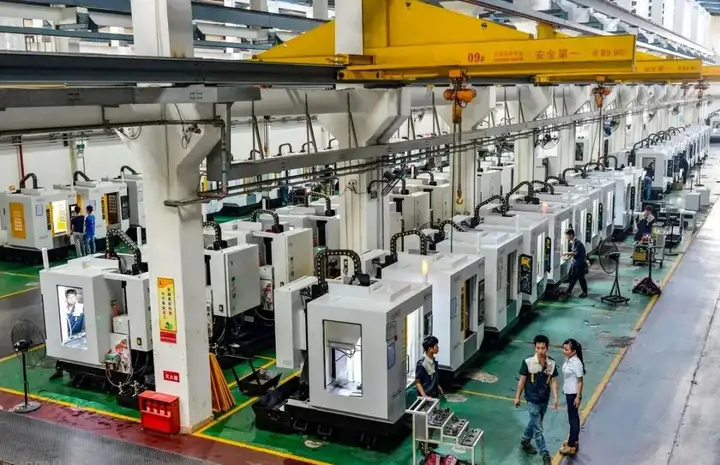
一、困境重重:传统生产模式的弊端
1、传统机械加工企业,往往存在过量生产的问题。
就拿一家生产汽车零部件的机械加工厂来说,为了应对旺季订单,在淡季时就大量生产零件。可市场需求多变,旺季一过,仓库里积压了大量卖不出去的零部件。
这些库存不仅占用巨额资金,还堆满了仓库,导致场地紧张。而且零部件存放久了,还可能生锈、损坏,只能报废处理,损失惨重。
2、等待浪费在这类企业也屡见不鲜
工人常常因为原材料供应不及时,只能停工等待。设备一旦出故障,整个生产线就得停滞,维修时间长,生产计划被打乱。
曾有一家阀门加工企业,因设备老化,频繁出现故障,每次维修都要耗费好几天,一个月下来,因设备故障导致的停工时间就多达一周,严重影响了产量和交货期。
3、运输环节也是浪费的 “重灾区”
一些机械加工厂内部布局混乱,原材料从仓库运到加工车间,要经过多个迂回路线,耗费大量人力、时间,运输途中零部件还容易磕碰受损。比如一家农机具加工企业,厂区面积大,但布局不合理,物料搬运距离长,每年光是运输成本就高得惊人,还影响了生产效率。
4、库存管理更是让企业头疼不已
为了避免原材料短缺影响生产,企业大量囤积原材料。像一家生产机床配件的企业,大量囤积钢材,结果部分钢材因存放时间过长生锈变质,无法使用,只能扔掉,造成极大浪费。
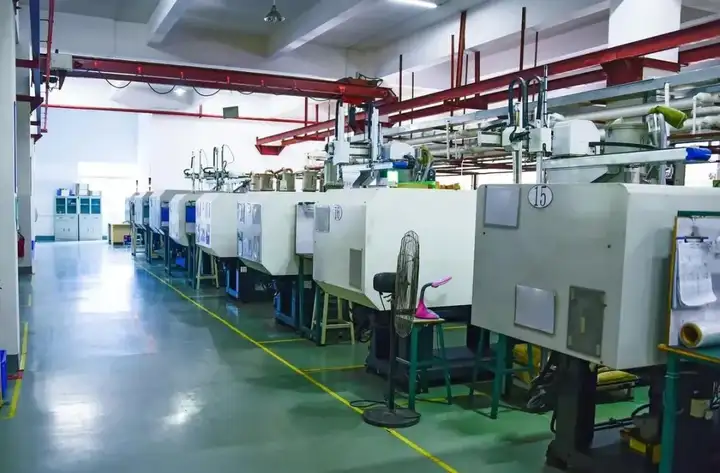
二、精益曙光:转型的关键步骤
1、价值流分析:精准定位问题
精益生产转型的第一步,就是进行价值流分析。通过绘制价值流图,企业能清晰看到产品从原材料到成品的整个生产流程,找出其中不增值的环节。
例如,一家齿轮加工企业在做价值流分析时发现,产品检验环节流程繁琐,存在多次重复检验,耗费大量时间和人力。于是,企业重新优化检验流程,减少不必要的检验步骤,提高了生产效率。
2、拉动式生产:以需求为导向
切换到拉动式生产模式,对机械加工企业至关重要。企业要根据客户订单来安排生产,避免盲目生产。
某机械零件定制企业,以前按预测生产,库存积压严重。转型后,采用拉动式生产,客户下单后才开始生产,库存大幅减少,资金周转率显著提高。
3、5S 管理:打造整洁高效车间
5S 管理(整理、整顿、清扫、清洁、素养)能有效改善车间环境,提高生产效率。有一家小型机械加工厂,车间原本杂乱无章,工具、原材料随意摆放,工人找工具和物料常常花费大量时间。
实施 5S 管理后,车间变得整洁有序,工具和物料都有固定摆放位置,工人工作效率大幅提升。
4、持续改善:永不止步的追求
持续改善是精益生产的核心。企业要鼓励员工积极提出改进建议,不断优化生产流程。
一家机械加工企业设立了 “持续改善奖励制度”,员工提出的关于优化加工工艺、减少浪费的建议,一旦被采纳,就能获得奖励。这激发了员工的积极性,企业生产效率不断提高,成本持续降低。
成功案例:某机加工企业的华丽蜕变
某机加工企业曾经也是一家深陷困境的机械加工企业,生产成本高,产品质量不稳定,市场份额逐渐萎缩。在决定进行精益生产转型后,企业首先对生产流程进行全面梳理,实施价值流分析,找出了大量浪费环节。
通过优化布局,将相关工序集中,缩短了物料运输距离。引入拉动式生产模式,库存积压减少了 70%。开展 5S 管理,车间环境焕然一新,生产效率提高了 50%。持续改善活动的开展,让企业每年节约成本数百万元。
如今,该企业已成为行业内的标杆企业,产品质量和生产效率都处于领先地位。
机械加工企业要想在激烈的市场竞争中脱颖而出,精益生产转型势在必行。
从认识传统生产模式的弊端,到实施价值流分析、拉动式生产、5S 管理等关键步骤,再到持续改善,每一步都是企业走向成功的基石。
记住,精益生产不是一时的潮流,而是企业持续发展的必由之路。只有不断消除浪费,提升效率,才能在市场浪潮中站稳脚跟,驶向成功的彼岸。