"王总,这是本月第三次客户投诉了!" 质量经理把报表摔在桌上,会议室里的空气瞬间凝固。
这不是个例。据《2024 中国制造业质量白皮书》显示,87% 的企业存在质量改善虎头蛇尾的现象。为什么投入大量资源,质量问题却像韭菜一样割了又长?
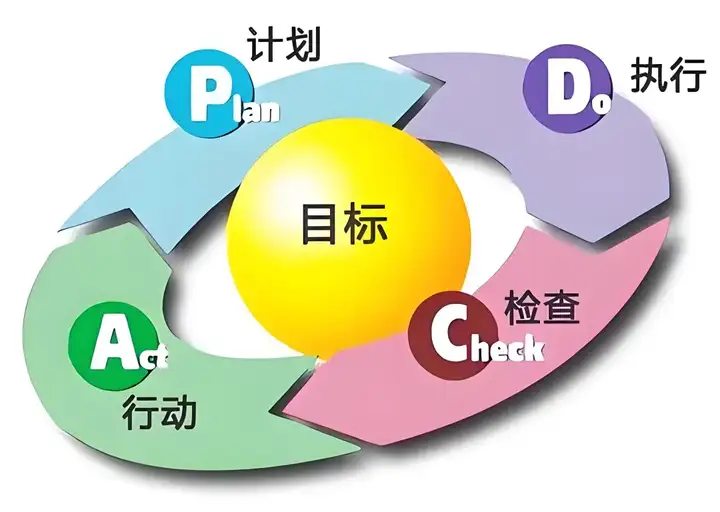
答案就藏在精益生产的 "永动机"——PDCA 循环里。
一、从 "头痛医头" 到系统破局(Plan 阶段)
某汽车零部件企业曾遇到刹车盘异响问题,工程师们连续三个月拆换零件却毫无进展。直到引入 PDCA 循环后,他们做了三件事:
-
绘制价值流程图,发现 90% 的问题出在热处理环节
-
建立 5M1E 分析表,锁定冷却液配比偏差
-
设定 "异响率下降 50%" 的 SMART 目标
这个阶段的核心是:把经验判断转化为数据驱动的系统分析。记住,好的计划是成功的 80%。
二、让改善落地生根(Do 阶段)
在执行环节,某电子厂创造了 "三色标签法":
-
红色标签:立即整改的安全隐患
-
黄色标签:48 小时内解决的质量问题
-
蓝色标签:需跨部门协作的改善项目
这种可视化管理让执行效率提升 40%。关键要记住:改善方案必须具备可操作性,就像丰田的 "五个为什么" 分析法,要挖到问题的根本原因。
三、建立质量雷达系统(Check 阶段)
某家电企业的做法值得借鉴:
-
安装在线检测传感器,实时监控 127 个质量参数
-
每周生成 "质量健康指数" 仪表盘
-
每月召开 "红牌作战" 会议,公示 TOP5 问题
数据显示,引入 PDCA 循环后,该企业客户投诉率从 2.3% 骤降至 0.4%。检查阶段的精髓在于:用客观数据替代主观判断,建立持续改进的反馈机制。
四、从经验到标准的进化(Act 阶段)
某医疗设备制造商的案例堪称经典:
-
将有效改善措施纳入作业指导书(SOP)
-
开发防错装置(Poka-Yoke)固化成果
-
建立 "改善知识库" 供全员学习
这个阶段最容易被忽视,却是 PDCA 循环的灵魂。就像戴明博士所说:"没有标准化,就没有改善的持续。"
现在,让我们回到文章开头的案例。那家汽车零部件企业通过完整的 PDCA 循环,不仅解决了异响问题,更建立了持续改进的机制。三个月后,客户投诉归零,生产效率提升 25%。