一、成本降低的隐形战场
2025年1月,某家电巨头因实施持续改善项目,年度成本降低12.3亿元,利润率提升4.7%。这一数据背后,揭示了一个被长期忽视的真相:持续改善不是短期行为,而是长期成本降低的战略引擎。
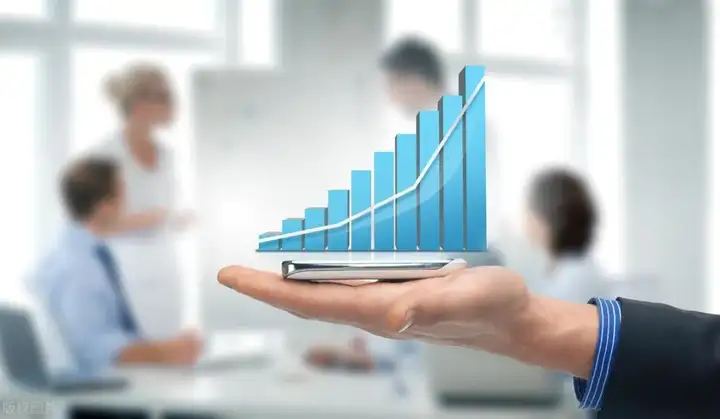
数据震撼:
-
全球制造业因持续改善带来的成本节约年均超1200亿美元(《2025全球制造业成本白皮书》)
-
精益标杆企业通过持续改善,生产成本年均降低8%-12%(麦肯锡研究报告)
-
某汽车零部件企业通过改善活动,单件成本下降23%,年节约成本超5亿元
二、持续改善的四大降本逻辑
1. 消除浪费:从显性到隐性
-
七大浪费的数字化识别:
✓ 过量生产:通过智能排程减少库存积压(某电子厂库存周转率提升3倍)
✓ 等待时间:通过实时监控减少设备闲置(某机械厂设备利用率提升至92%)
✓ 运输浪费:通过优化布局减少物流距离(某食品厂物流成本下降18%) -
隐性浪费的量化分析:
✓ 动作浪费:通过动作分析减少无效操作(某装配线效率提升35%)
✓ 管理浪费:通过流程优化减少审批环节(某化工企业审批周期缩短60%)
2. 流程优化:从局部到全局
-
价值流图(VSM)的应用:
✓ 识别瓶颈工序:某汽车厂通过VSM分析,将生产周期从12天缩短至7天
✓ 优化信息流:某电子厂通过信息化改造,订单交付周期缩短40% -
全流程协同改善:
✓ 跨部门协作:某家电企业通过跨部门改善小组,将新品开发周期缩短30%
✓ 供应链协同:某机械厂通过供应商协同改善,采购成本下降15%
3. 技术创新:从传统到智能
-
数字化工具的引入:
✓ 数字孪生:某航空企业通过虚拟调试,减少80%的试制返工
✓ 人工智能:某制药厂通过AI预测性维护,设备故障率下降60% -
自动化与智能化升级:
✓ 机器人应用:某电子厂通过自动化改造,人工成本下降25%
✓ 智能检测:某汽车厂通过AI视觉检测,漏检率降至0.01%
4. 文化驱动:从被动到主动
-
全员参与的改善文化:
✓ 改善提案制度:某化工企业年人均提案数达12件,累计节约成本1.2亿元
✓ 改善激励机制:某机械厂通过积分奖励,改善项目完成率提升至95% -
持续学习的组织能力:
✓ 精益培训体系:某电子厂通过系统培训,培养精益骨干200人
✓ 知识管理平台:某汽车厂通过知识库建设,改善经验共享效率提升50%
三、持续改善的长期价值
1. 成本结构的根本性优化
-
从"降本"到"价值创造":通过持续改善,企业不仅降低现有成本,还能优化成本结构,提升长期竞争力
-
案例:某家电企业通过改善活动,将研发成本占比从12%降至8%,同时新产品上市周期缩短30%
2. 组织能力的持续提升
-
从"改善项目"到"改善基因":持续改善不仅带来成本节约,还能培养组织的自我优化能力
-
案例:某汽车零部件企业通过持续改善,年人均效率提升15%,员工流失率下降20%
3. 市场竞争力的持续增强
-
从"价格竞争"到"价值竞争":通过持续改善,企业不仅能降低成本,还能提升产品价值,增强市场竞争力
-
案例:某机械厂通过改善活动,将产品不良率降至0.1%,客户满意度提升至98%
四、实战案例:丰田的"改善基因"
-
痛点:传统生产模式下,成本居高不下,市场竞争力不足
-
创新方案:
-
建立全员参与的改善文化,年人均提案数达10件
-
引入数字化工具,实现全流程的实时监控与优化
-
成果:
✓ 生产成本年均降低8%-12%
✓ 产品不良率降至0.05%
✓ 市场占有率提升至25%
五、行动路线图
-
立即行动:建立持续改善的组织架构,明确目标与责任
-
技术升级:2025年内完成关键工序的数字化改造(推荐SAP Lean Management平台)
-
文化驱动:开展全员参与的改善活动,建立激励机制
-
持续优化:建立改善效果的评估体系,持续优化改善流程
未来已来:当持续改善成为组织的基因,当每一名员工都成为改善的推动者,这场关乎制造业生死的隐形战争,正在重新定义成本竞争的底层规则。