在工厂生产的舞台上,设备就是主角,它们一旦 “闹脾气” 发生故障,整个生产流程就可能陷入混乱。而精准找出设备故障的根源,就如同为生病的主角诊断病因,是恢复生产秩序的关键。今天,我们就来聊聊在设备故障根因分析中极为有效的 TPM 方法。
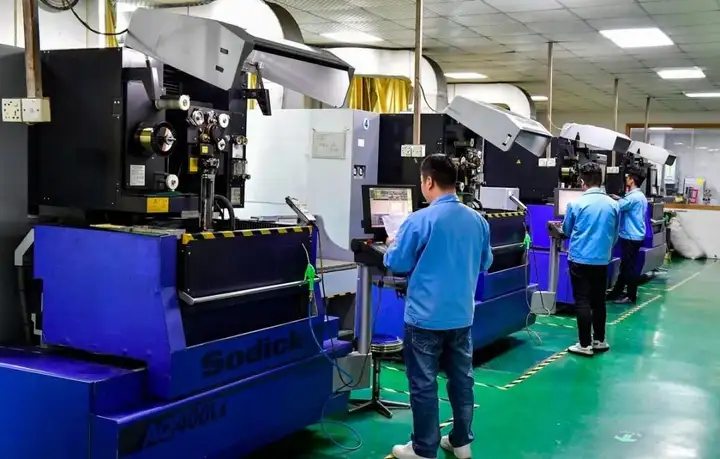
一、TPM 方法:全面生产维护的智慧结晶
TPM,即 Total Productive Maintenance,全面生产维护,它倡导全员参与,从设备的规划、设计、使用到维护的全生命周期进行管理,旨在追求设备综合效率最大化。
在设备故障根因分析领域,TPM 方法凭借其系统性和全面性,成为众多企业的得力助手。
TPM 方法强调预防为主,通过日常的设备检查、清洁、润滑、紧固等保养工作,及时发现设备潜在问题,将故障隐患扼杀在萌芽状态。同时,当故障不幸发生时,TPM 也提供了一套科学严谨的分析流程,帮助我们抽丝剥茧,找到故障的真正根源。
二、TPM 方法在设备故障根因分析中的实战应用
案例一:某汽车零部件加工厂
在一家汽车零部件加工厂,一台关键的冲压设备频繁出现冲压件尺寸偏差的问题。起初,维修人员只是简单地调整设备参数,但问题依旧反复出现。后来,该厂引入 TPM 方法进行故障根因分析。
首先,成立了由设备操作人员、维修人员、工艺工程师组成的 TPM 小组。小组成员通过对设备运行数据的详细记录和观察,发现设备在运行一段时间后,冲压模具的温度会异常升高。
进一步检查发现,模具的冷却系统存在堵塞,冷却液流通不畅,导致模具温度过高,进而影响冲压件尺寸。
找到问题根源后,TPM 小组一方面对冷却系统进行全面清理和维护,确保冷却液正常循环;另一方面,制定了严格的设备日常检查制度,要求操作人员每班都要检查冷却系统的运行状况。实施这些措施后,冲压设备的故障发生率大幅降低,产品质量得到了显著提升。
案例二:电子制造企业的 SMT 生产线
一家电子制造企业的 SMT 生产线经常出现贴片机抛料现象,严重影响生产效率。企业运用 TPM 方法展开深入分析。
TPM 小组成员从人、机、料、法、环五个方面入手。在人员方面,检查操作人员的操作规范,发现部分新员工对设备操作不够熟练,在更换物料时动作不规范,容易导致物料偏移,从而引发抛料。
在设备方面,对贴片机进行全面检查,发现吸嘴磨损严重,影响了对物料的吸取精度。
在物料方面,经过检验,发现部分物料的包装不符合标准,导致物料在送料过程中出现卡顿。
在方法方面,优化了贴片机的编程参数,使其更适应不同类型物料的贴装要求。
在环境方面,改善了车间的温湿度控制,避免因环境因素影响物料的性能。
通过对这些问题的逐一解决,SMT 生产线的抛料率从原来的 5% 降低到了 1% 以内,生产效率大幅提高。
三、TPM 方法应用的关键要点
-
全员参与:TPM 强调全员参与,只有操作人员、维修人员、管理人员等各部门人员共同协作,才能全面收集设备信息,准确找出故障根因。
-
数据收集与分析:详细记录设备运行数据,包括温度、压力、转速等,以及故障发生时的具体情况,通过对这些数据的深入分析,为故障根因判断提供有力依据。
-
持续改进:设备故障根因分析不是一劳永逸的,企业要根据实际情况,不断优化 TPM 方法的应用,持续改进设备管理水平。
在设备故障根因分析的道路上,TPM方法为我们点亮了一盏明灯。它以其科学的理念和实用的方法,帮助企业快速、准确地找出设备故障根源,提升设备运行效率,保障生产的顺利进行。