精益管理示范区案例
按照中船集团第七一六研究所精益管理工作推进计划,制造部部件装配班组以打造精益管理示范区为目标,以“冲锋队”为先锋,践行“降本增效,品质领跑”口号,全员投入精益改善行动。在短时间内,团队高效完成27项改善任务,形成八大创新成果,并在全所第1期精益管理示范区打造成果发表会上斩获金奖,成为精益管理标杆典范!
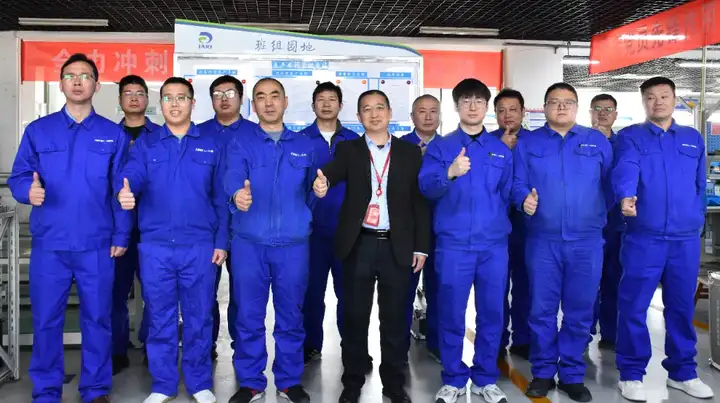
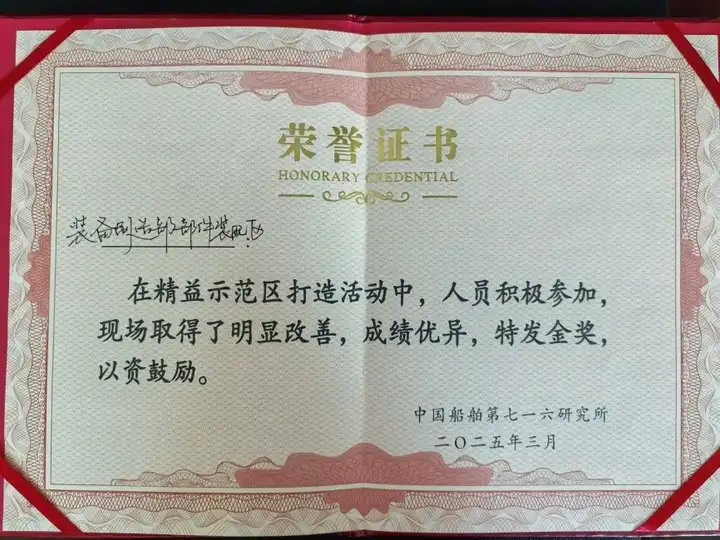
冲锋在前,精益改善全面落地
班组成员群策群力,直面生产痛点,精准施策,推出八大亮点举措,实现效率与品质双提升。
1.管理看板动态管控:将月计划分解为日计划,实时跟踪订单进度,急件生产一目了然,及时管理订单闭环,质量监督透明高效。
2.工艺文件“抬头即见”:工艺手册变身工位看板,实现工艺标准化,作业效率与质量双提升。
3.工具“三定”管理:工具定位、定容、定量,实现工具快速取用,作业效率显著优化。
4.废旧材料巧用技防:利用废旧泡沫自制产品防护工装,降低产品磕碰风险,实现“零成本技防”。
5.物料限量标识管理:限量标识卡+图示化管理,实现库存控制优化,两金压降成效突出。
6.装配分区精细作业:机箱、模块、插件及零星产品分区作业,质量稳定性增强,错装率趋近于零。
7.SOP标准化操作:推行SOP操作程序,工艺文件细化至工步级,保障产品一致性。
8.流水脉动式作业:流水线团队合作生产模式,每个人负责产品的一个部件装配任务,极大的提高了生产效率。
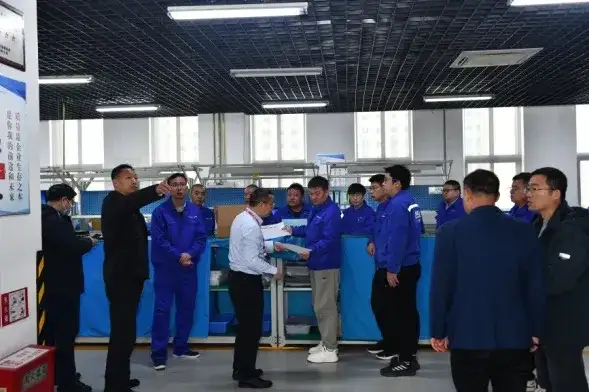
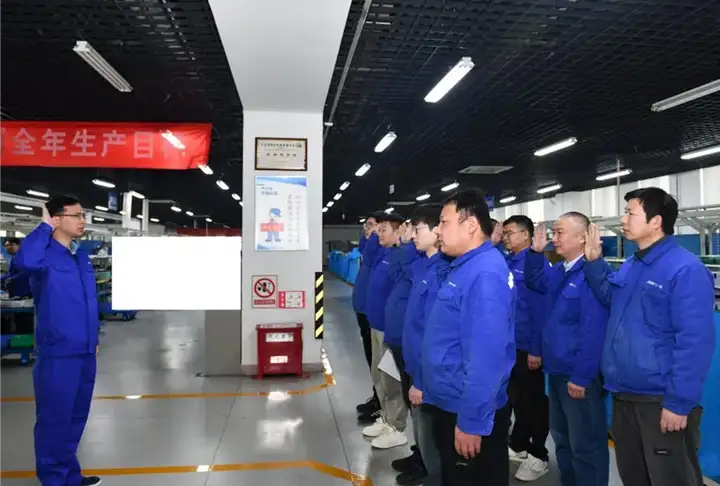
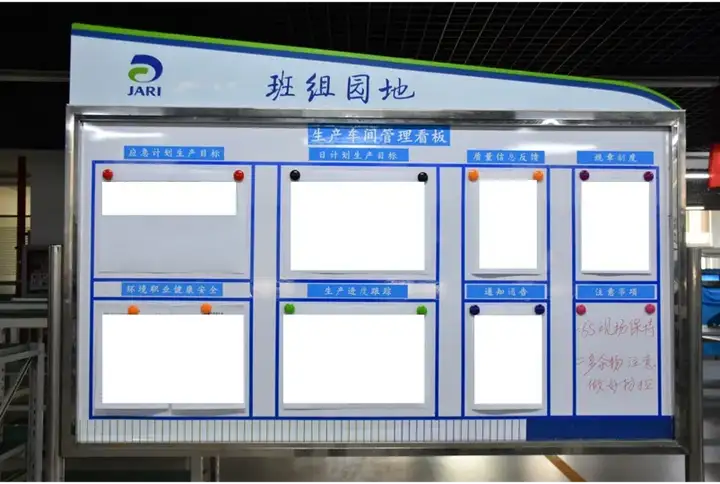
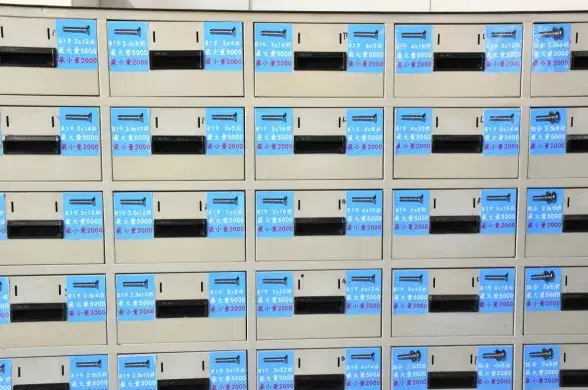
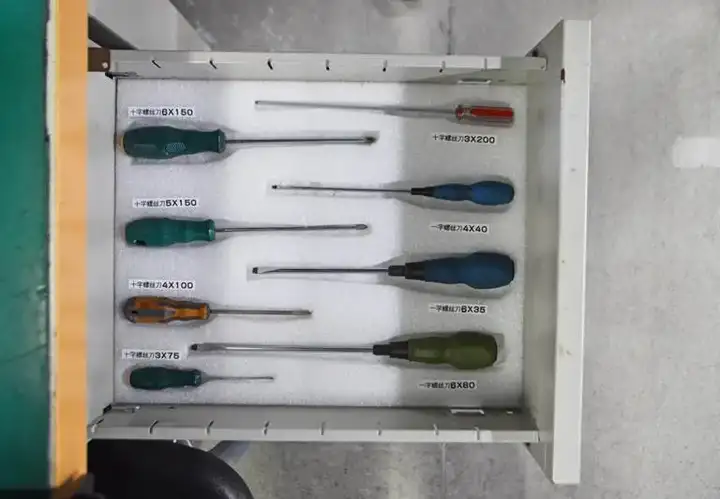
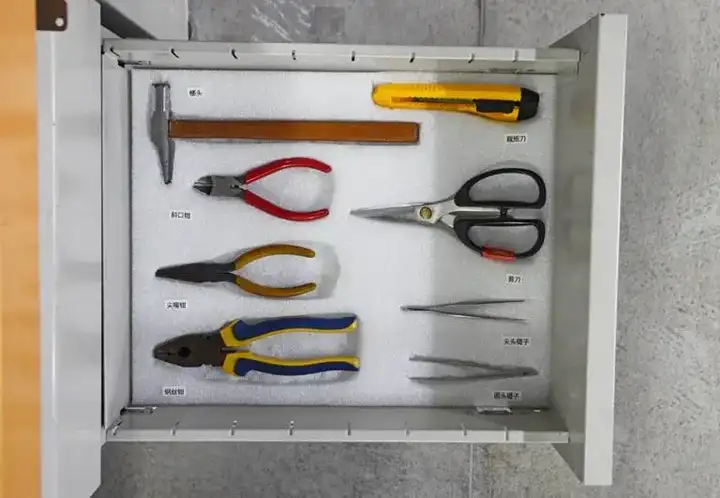
文化焕新,提升全员参与信心
为营造”人人参与、持续改进”的文化氛围,示范区班组成员通过多项举措激发员工主动性。建立精益管理提案制度,鼓励全员针对生产流程、工具使用等方面提出改善建议,累计收集提案50余条,形成“人人有责任、事事可优化”的参与机制;选树标杆榜样,定期评选“精益之星”,公开表彰优秀提案者,形成“比学赶超”的精益改善氛围;透明化反馈机制,利用管理看板实时展示改善成果与进度,增强员工对改善成效的直观感知,提升参与信心。
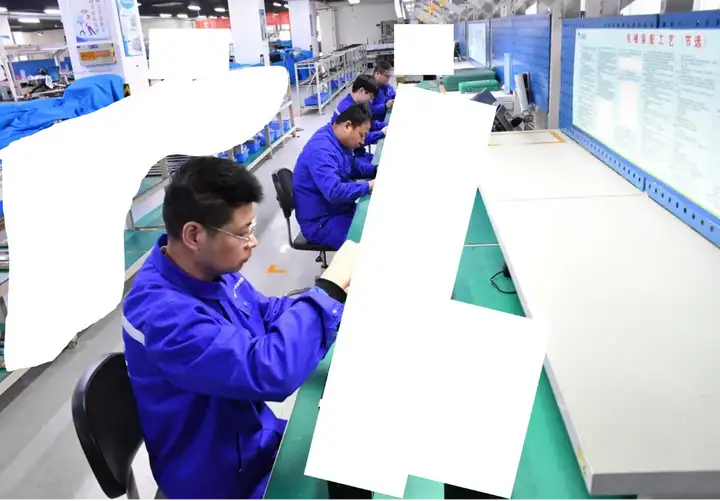
通过以上措施,团队文化实现三大蜕变:一是理念扎根。员工从“精益改善费时费力”的抵触心态,转变为主动思考“如何优化流程、创造价值”;二是角色转变。通过提案制度,全员从“被动执行者”升级为“改善主导者”,车间内“抢提方案、争当标杆”蔚然成风;三是氛围凝聚。形成“改善无大小、创新无止境”的共识,真正实现从“要我精益”到“我要精益”的文化跃迁。
乘胜追击,精益之火全面燎原
为进一步巩固深化并推广精益管理示范区创建成果,制造部积极探索成立“精益推广小组”,每月组织跨车间跨工序交流,输出标准化改善手册;启动“全员通关”计划,开展精益管理理论课程培训,夯实精益技能基础,确保一线员工100%掌握精益工具;推进数字化精益看板建设,实现生产数据实时监控,打造透明化精益管理平台。
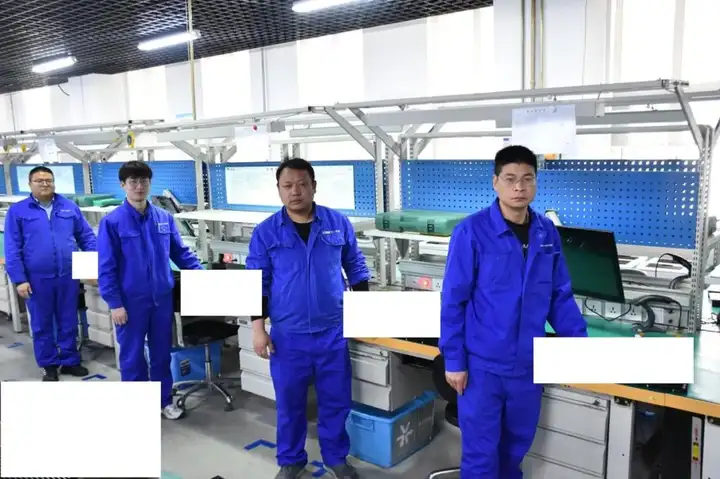
班组成员纷纷表示,将以此次活动为契机,以“零浪费、零缺陷”为目标,持续深化精益管理实践,激发创新活力,赋能科研生产,为产品制造提质增效贡献力量,为七一六所高质量发展注入更强动能!