在竞争激烈的市场环境中,产品质量是企业立足的根本。然而,许多企业陷入一个误区,认为提升质量必然伴随着成本的大幅上升。
事实真的如此吗?精益生产理念为我们打开了新的思路,它强调通过优化流程、消除浪费,在不额外增加成本的情况下显著提升产品质量。今天,就让我们一同探寻这些神奇的精益方法与实践。
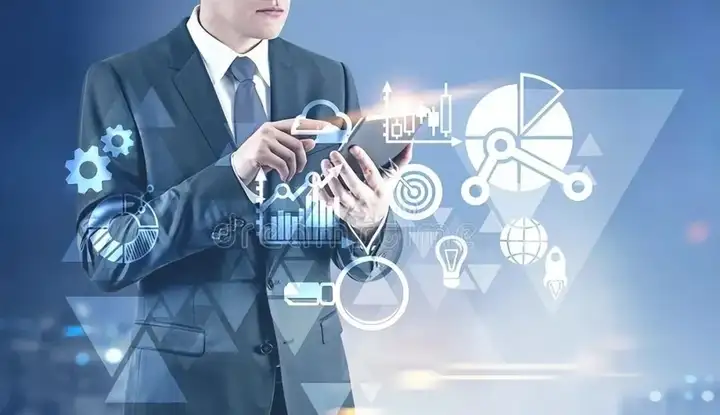
一、精益思维:质量与成本并非对立
传统观念里,投入更多资金购买更优质的原材料、引进高端检测设备似乎是提升质量的必经之路。但精益思维却另辟蹊径,它认为质量问题往往源于生产过程中的各种浪费,如过度加工、等待时间、库存积压等。
这些浪费不仅消耗资源,还隐藏着质量隐患。当我们运用精益方法消除这些浪费时,质量问题也会随之减少,同时成本也得以控制。
二、精益方法助力质量提升:案例见证
案例一:A企业的流程优化奇迹
A企业是一家电子产品组装企业。过去,产品不良率一直居高不下,客户投诉频繁。企业管理层原本打算投入大量资金更换生产设备来改善质量,但在引入精益生产方法后,决定先对生产流程进行全面梳理。
通过价值流分析,他们发现生产线上存在大量不必要的操作步骤。例如,某些零部件在组装前要经过多次重复检测,不仅浪费时间,还增加了人为损坏的风险。于是,企业精简了检测流程,将部分检测环节整合到组装工序中,同时制定了标准化作业流程,确保每个工人的操作一致。
这一系列改进措施实施后,产品不良率从原来的 15% 骤降至 5%,生产效率提升了 30%。令人惊喜的是,整个改进过程几乎没有增加额外成本,仅仅是通过优化现有资源的配置就实现了质量与效率的双重飞跃。
案例二:B企业的库存管理变革
B企业是一家机械制造企业,长期以来面临着库存积压和产品质量不稳定的问题。库存中大量的原材料和半成品不仅占用了大量资金,还因长时间存放导致部分材料性能下降,影响产品质量。
在实施精益方法时,企业引入了准时化生产(JIT)理念,与供应商建立了紧密的合作关系,实现了原材料的准时配送。同时,运用看板管理系统,实时监控生产线上的物料需求,避免了过度生产和库存积压。
随着库存的减少,企业能够及时使用新鲜的原材料进行生产,产品质量得到了显著提升。因库存管理优化释放的资金,企业用于员工技能培训,进一步保障了生产质量的稳定性。这一变革不仅未增加成本,反而通过降低库存成本和减少次品损失,为企业节省了大量资金。
三、提升质量不增成本的精益实践要点
1、价值流分析:绘制完整的价值流图,识别生产过程中的增值与非增值环节。去除那些不增加价值却消耗资源的步骤,如不必要的搬运、等待时间等,从而简化流程,降低出错概率,提升质量。
2、标准化作业:制定详细、明确的标准化作业流程,确保每个员工在相同的操作环节都遵循统一标准。这有助于减少人为因素导致的质量差异,提高产品一致性,同时也便于新员工快速上手,提升整体生产效率。
3、全员参与质量控制:培养全体员工的质量意识,让每个人都成为质量的守护者。鼓励一线员工及时反馈生产中的质量问题,并赋予他们解决问题的权力和能力。通过全员参与,能够在第一时间发现并解决质量隐患,避免问题扩大化。
4、持续改善:建立持续改善的企业文化,鼓励员工不断提出改进建议。定期对生产过程进行评估和优化,小步快跑地持续提升质量。这种持续的微创新积累起来,能够带来显著的质量提升效果,且无需大规模的资金投入。
在精益的世界里,质量与成本并非天平的两端,而是携手共进的伙伴。以精益之法雕琢生产流程,质量提升的曙光将照亮成本控制的道路,引领企业驶向卓越。