精益领域提倡用一整套成熟的系统方法得到想要的结果。其优势是步骤性强,可以被大量复制,还能保证输出最好的结果。这也是精益工具中梦寐以求的步骤化操作方法和过程的操作指引,适用于大量的生产企业。无论是在汽车行业还是在电子行业,都能保证企业内部的改善人员可以轻松地使用精益的相关工具。
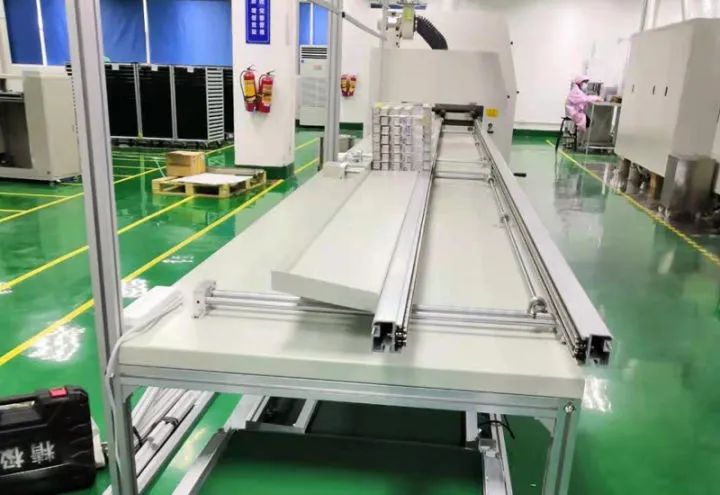
单元生产线的设计、实施过程步骤化的好处就像使用一台“傻瓜相机”,不仅操作简单,而且产出效果佳。在“守、破、离”三个阶段,如果你在“守”的阶段用参照步骤搭建单元生产线,就可以减少每个步骤中因为摸索而消耗的时间,可以不用思考建立单元生产线,而把大量的经理直接用于每个操作步骤。如果是在“破”的阶段,你可以独立建立自己单元化设计的标准步骤,如果是在“离”的阶段,你可以天马行空地用“无招”的方式完成单元生产线设计。
—1—
第一步:改善对象选取
通常人们一听到要进行改善,机会立刻考虑各种改善方案,然后直接进行改善,并没有对改善对象进行选择。这种方式虽然对立即执行改善帮助很大,但有时会造成改善盲目且毫无头绪的状况。改善后,人们往往会发现如果改善另外一个对象,整体效果也许更加明显。
在寻找改善对象时,需要问以下问题:
1、改善对象是否合适?
2、改善能够带来巨大的收益吗?
3、改善是紧急且迫切的吗?
4、改善对象是领导关注的对象吗?
5、改善对象的选择有问题吗?
—2—
第二步:现状分析和浪费消除
现状分析是对改善对象的相撞把握,例如,客户需求(未来一年的需求/去年的需求、产品寿命周期、客户需求)、产品工艺流程(工艺流程、工艺特点、产品与零件)、产品组装(作业人员数量、工作台划分、生产平衡率、生产绩效表现、技能情况)、硬件条件(厂房、区域、设备、水电气共赢、照明)。这些都是在单元生产线设计前需要了解的信息。
除了掌握上面的信息,还需要进一步分析存在多少浪费,有多少改善点可以先改善,避免把浪费编制到新的生产线种。收集更多的信息不是目的,通过现状分析更多的问题,再设计出更加优秀的生产线才是目的。
—3—
第三步:“纸上谈兵”
“纸上谈兵”是单元生产线的真正设计阶段,需要设计生产线的整体线体、工作台、物料摆放及配送、现场生产线的布局。所有的设计都是在大脑或纸上完成的,所以企业将其称为“纸上谈兵”。
在“纸上谈兵”阶段,企业需要对人、物、设备、方法和环境5个方面进行综合考虑,即人员在什么样的环境中使用某种方法操作设备,完成物料的相应组装测试包装工作。
为了设计出更好的生产线,需要考虑3-5种备选方案,更多的备选方案可以提供更多的选择和不同的设计角度,最后可择优选择一种方案或者综合各种方案形成最终方案。如果企业只有能力完成一种单元生产线的设计,则可以邀请多家单元生产线设计方一起交流,得出更多不同的设计思路。
—4—
第四步:3P模拟设计
设计时需要考虑众多的因素,总有一些疏忽造成设计上的缺陷,如果在没有发现设计缺陷的情况下就让新生产线直接制造和试生产,则容易导致很多问题,以至于需要二次设计。如果想发现更多的设计缺陷,则需要增加一个设计验证的步骤,即生产准备流程模拟设计。
首先用简单的材料将设计好的单元线以实物展现出来;然后,围绕模拟简单生产线进行试生产;最后,全体成员一起讨论该过程种存在的设计缺陷。这样就可以用最小的代价消除设计缺陷,并且融入多人的考量设计出最合适的单元生产线。当然,如果你对设计很有信心,也可以省略这个步骤。
—5—
第五步:生产线试运行
新单元生产线设计好后就可以正式组织试运行了,在运行过程中一定会出现一些问题,需要一个改善支撑团队使用PDCA方法不断解决问题。如果没有改善团队的支持,作业人员就会认为新的单元生产线问题太多,不太适合公司的产品,从而倒退回原来的操作方式,使前面的工作白白浪费。
—6—
第六步:标准化
标准化是为了维持改善的现状,不让改善走回头路,同时将改善过程中的隐性知识用文化固化下来。
标准化也是一个PDCA不断循环的过程,即先制定相应的标准,作业人员按照标准作业,当作业人员发现更好的做法后修订新的标准,以便作业热暖按照新的标准作业执行,从而形成”标准-改善-标准”。
生产领域有很多标准文件,例如,操作手册、作业要领书、作业分解表、检查指导书、终检指导书、物料配送时间表、配送路径图等。